Paperless workshop
Remove the burden and constraints of a paper heavy shop floor! Your operators will be guided by electronic route cards and interactive work instructions.
Printing, it's out of date
« How long has this procedure been in place? » Don’t worry, you won’t hear this sentence again: only current valid instructions are active.
It's good to keep track of your production but Real time is better.
The information hunt is over. You know at all times where your production orders stand.
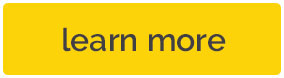
Learn more
Digitisation of industrial processes: when information becomes reliable
Digitisation allows information to be made available immediately and efficiently to all users concerned. It is therefore a prerequisite first step for any company oriented towards 4.0.
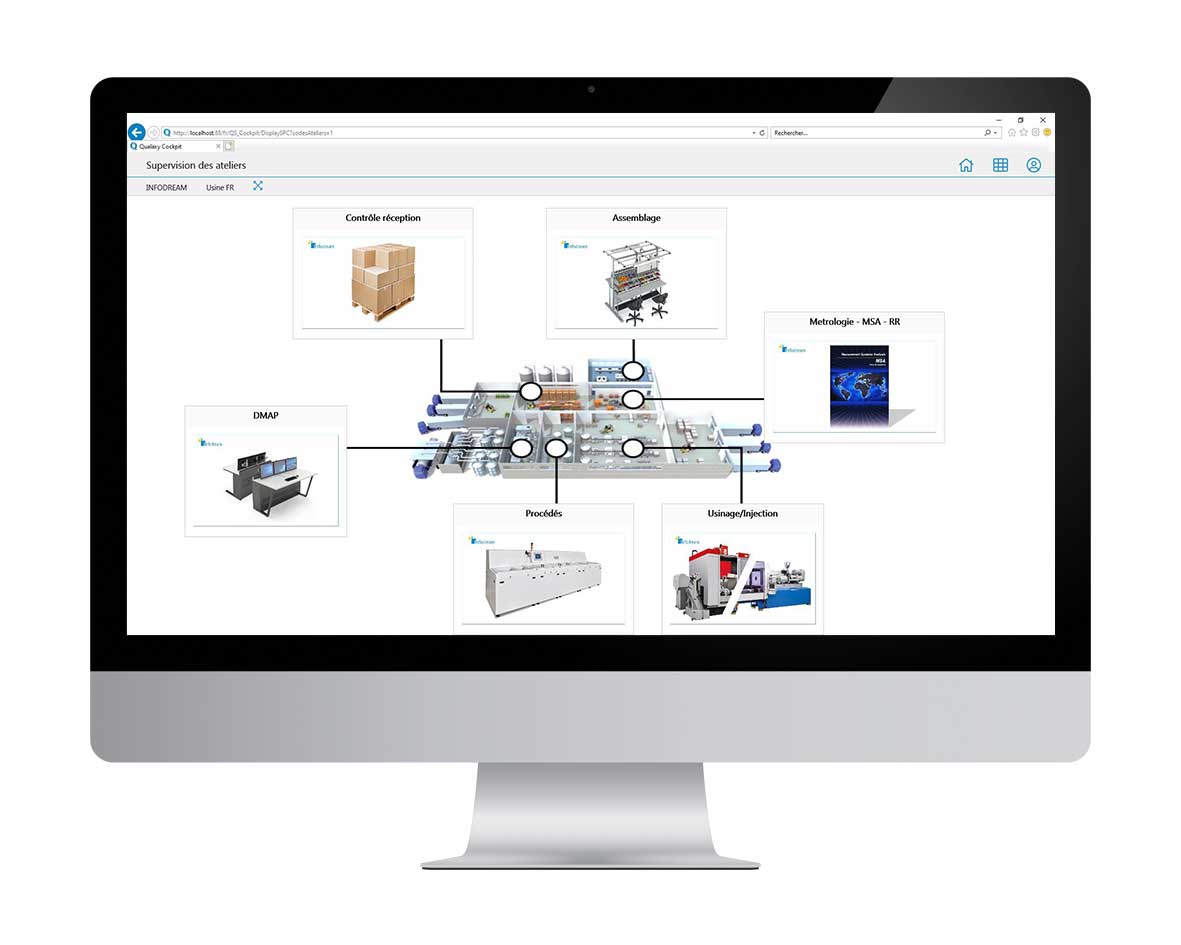
1/ The paperless workshop
In an industrial environment, paperwork is a source of information obsolescence, congestion and processing errors. On the other hand, the digital processing of information allows by definition an immediate and unequivocal availability of data.
2/ The right information at the right time
Correct information is only of interest if it is given at the time it is needed. The digitisation of processes enabled by the MES (Manufacturing Execution System) provides operators with the information they need, when they need it. They can thus focus on what makes them valuable: their industrial know-how.
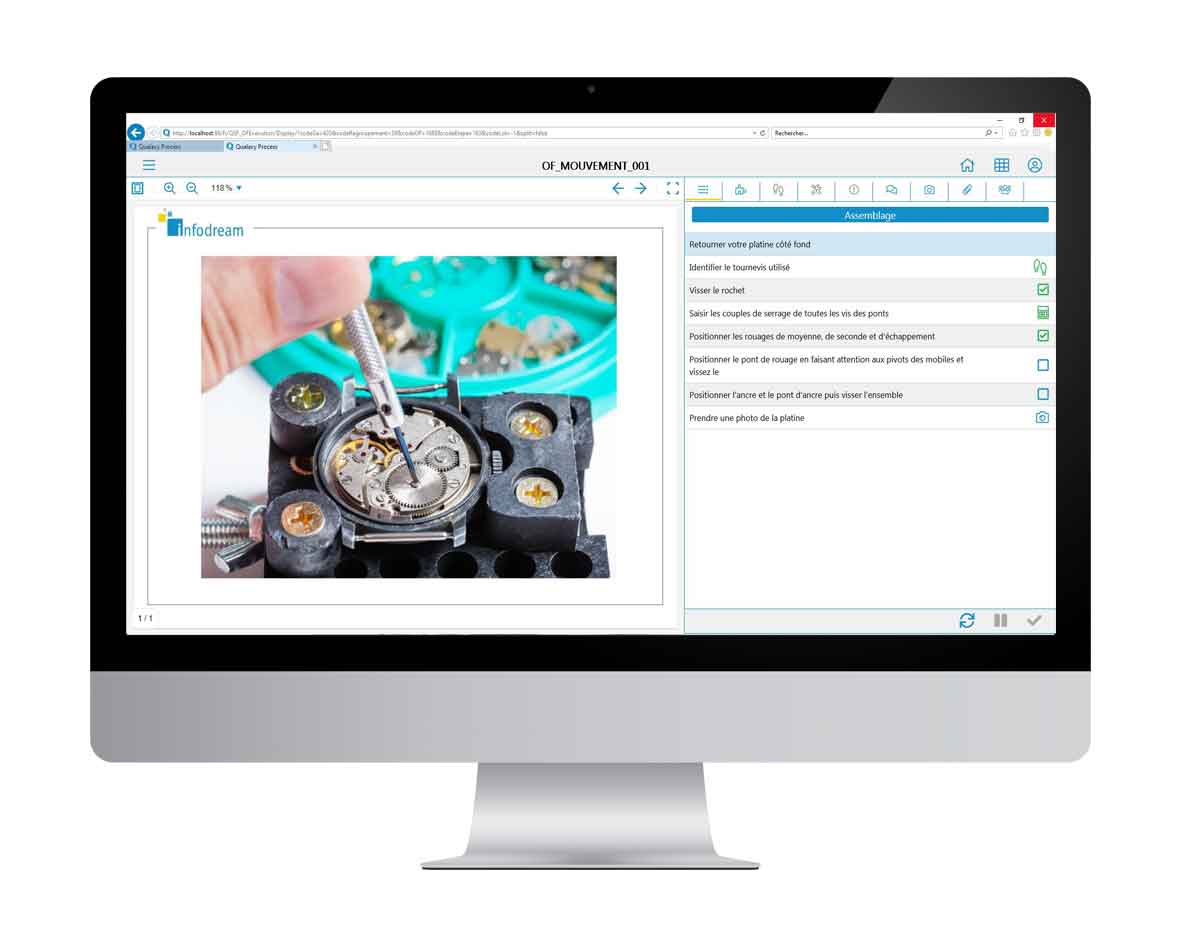
3/ Real-time monitoring of work in progress
The digitalisation of industrial processes, a digital link between the ERP and the workshop, makes it possible to visualise the status of the work orders in real time, and to share the data generated with all the stakeholders involved in the company’s production process.
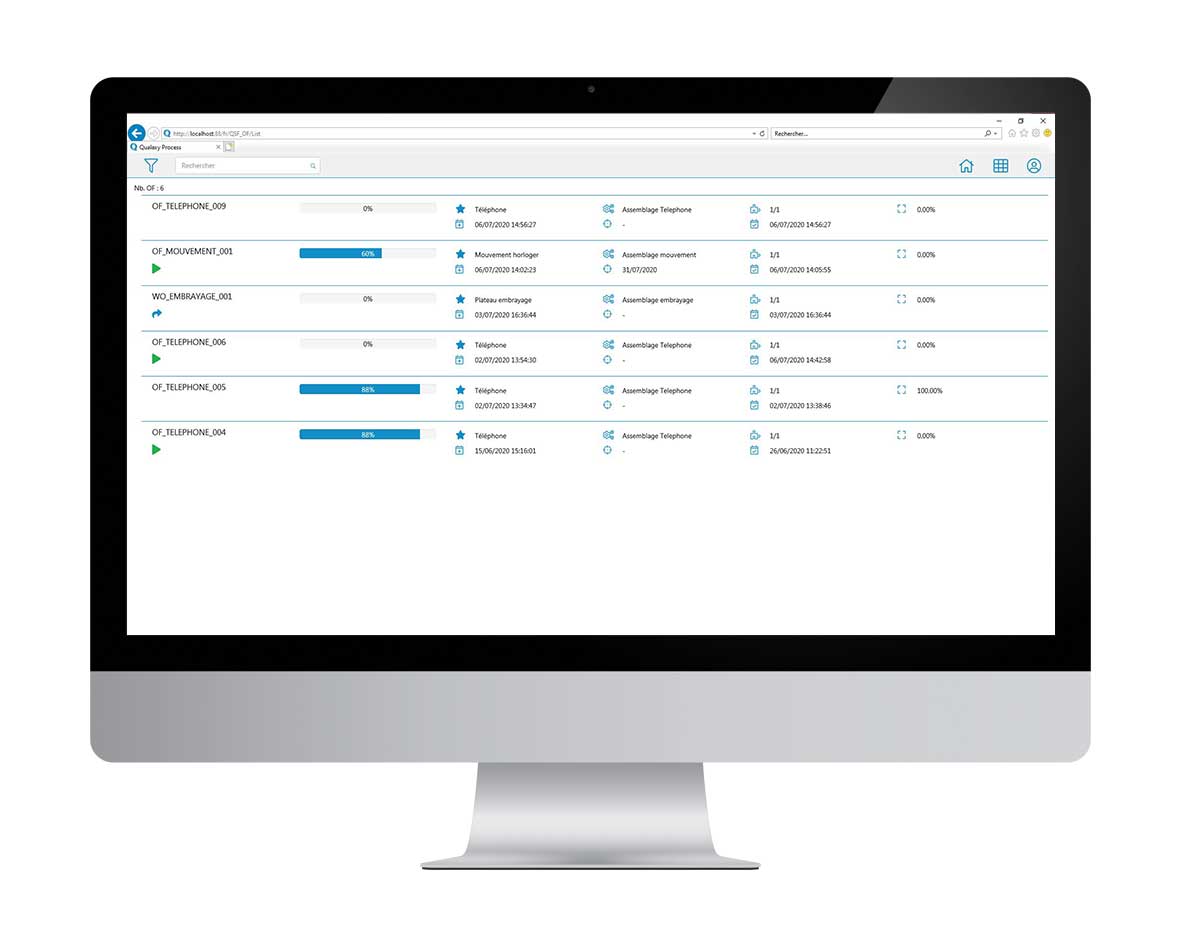
Not to be forgotten
Are you already convinced of the benefits of digitalisation? However, it is imperative that the chosen solution can be integrated into the company’s IT ecosystem. As the integration of the solution is an essential operation in any digitisation project, choosing a supplier recognised in the industrial environment remains a guarantee of security.
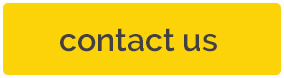
Paperless workshop
Remove the burden and constraints of a paper heavy shop floor! Your operators will be guided by electronic route cards and interactive work instructions.
Printing, it's out of date
« How long has this procedure been in place? » Don’t worry, you won’t hear this sentence again: only current valid instructions are active.
It's good to keep track of your production but Real time is better.
The information hunt is over. You know at all times where your production orders stand.

Learn more
Digitisation of industrial processes: when information becomes reliable
Digitisation allows information to be made available immediately and efficiently to all users concerned. It is therefore a prerequisite first step for any company oriented towards 4.0.
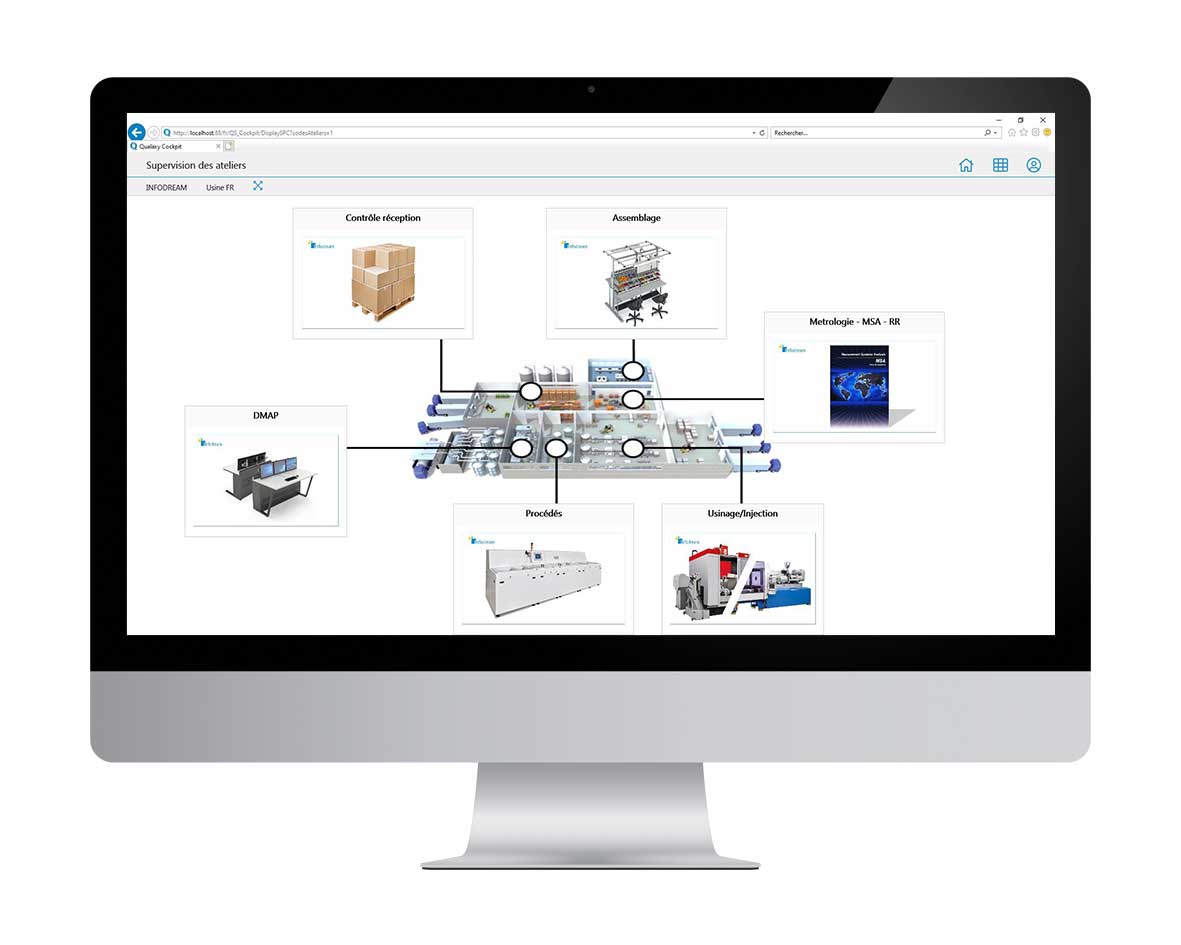
1/ The paperless workshop
In an industrial environment, paperwork is a source of information obsolescence, congestion and processing errors. On the other hand, the digital processing of information allows by definition an immediate and unequivocal availability of data.
2/ The right information at the right time
Correct information is only of interest if it is given at the time it is needed. The digitisation of processes enabled by the MES (Manufacturing Execution System) provides operators with the information they need, when they need it. They can thus focus on what makes them valuable: their industrial know-how.
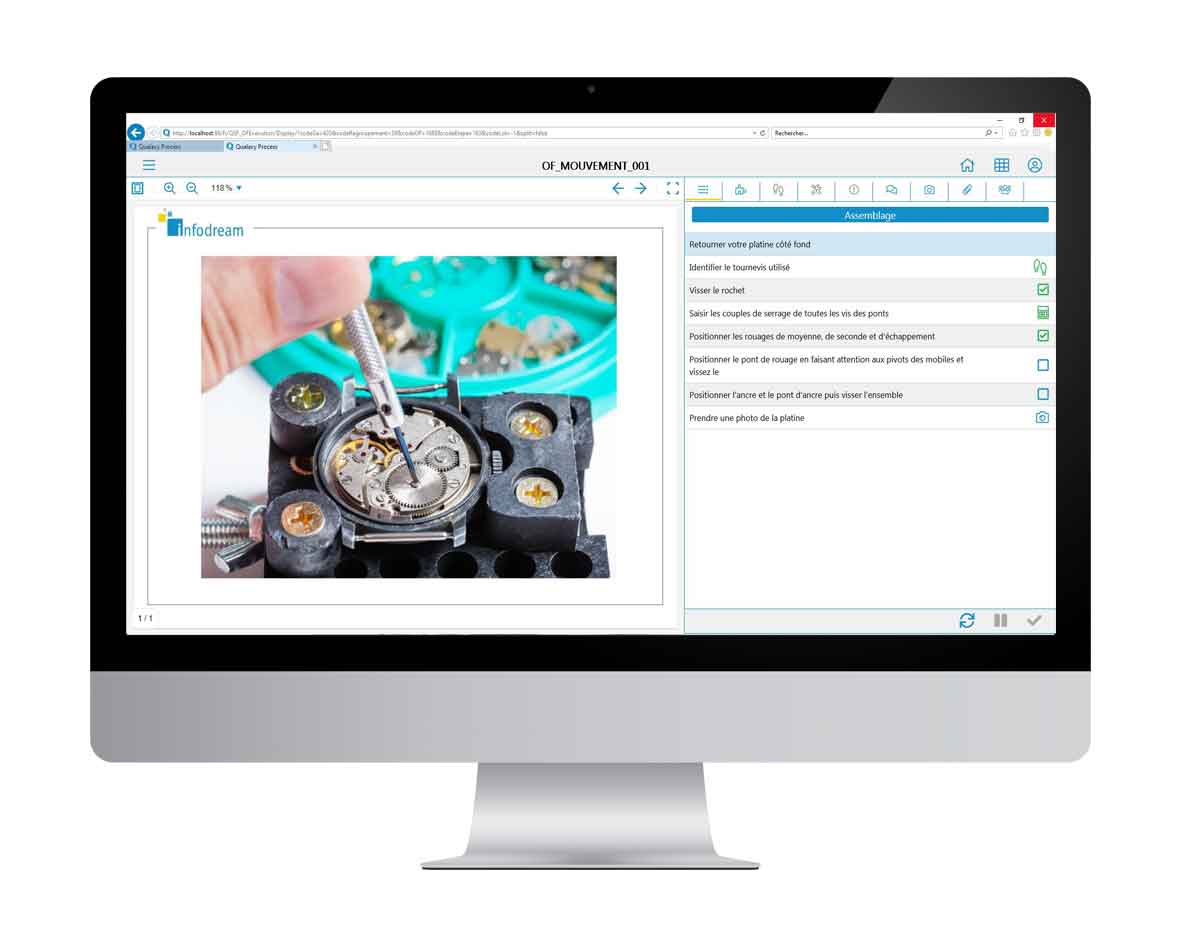
3/ Real-time monitoring of work in progress
The digitalisation of industrial processes, a digital link between the ERP and the workshop, makes it possible to visualise the status of the work orders in real time, and to share the data generated with all the stakeholders involved in the company’s production process.
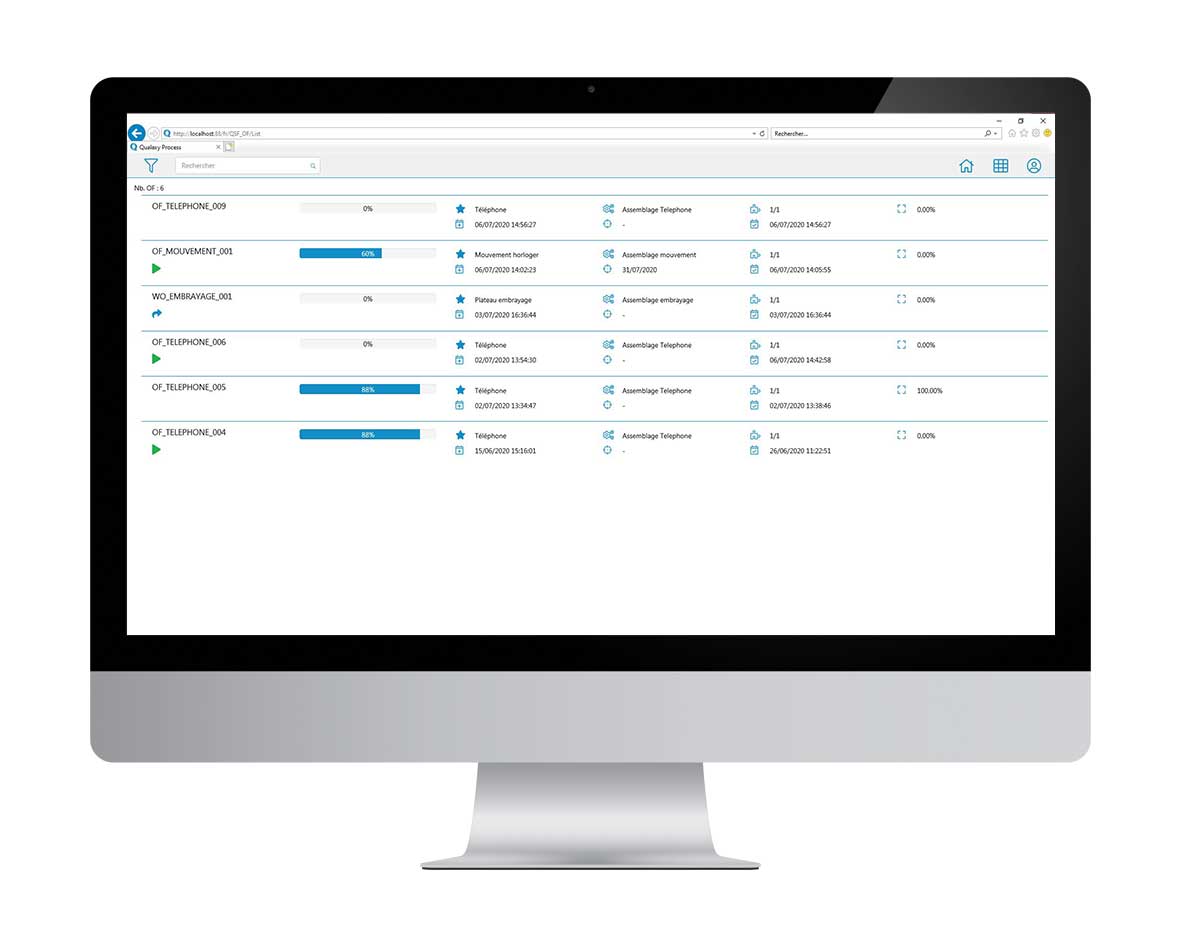
Not to be forgotten
Are you already convinced of the benefits of digitalisation? However, it is imperative that the chosen solution can be integrated into the company’s IT ecosystem. As the integration of the solution is an essential operation in any digitisation project, choosing a supplier recognised in the industrial environment remains a guarantee of security.
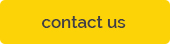
Total traceability
Every piece of information entered is recorded: you are sure to know who did what, when, where and how.
Quality standards
Our system meets many quality and regulatory requirements but you can also set up your own company standards.
"What version of the process was this?"
This question no longer needs to be asked: you keep a record all changes made to your processes.
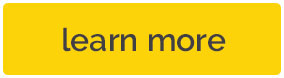
Learn more
Data traceability: beyond customer requirements
Depending on your business challenges, keeping track of the information associated with the manufacturing orders carried out in your workshop makes it easy to find all the parts that share the same defects, and simplifies the detection of the root causes in order to take the appropriate corrective measures.
1/ Who? What? When? Where?
Full traceability of the production process makes it possible to know exactly the operator(s) involved in the manufacturing process, the nature of the operations carried out, as well as the date and the industrial means used.
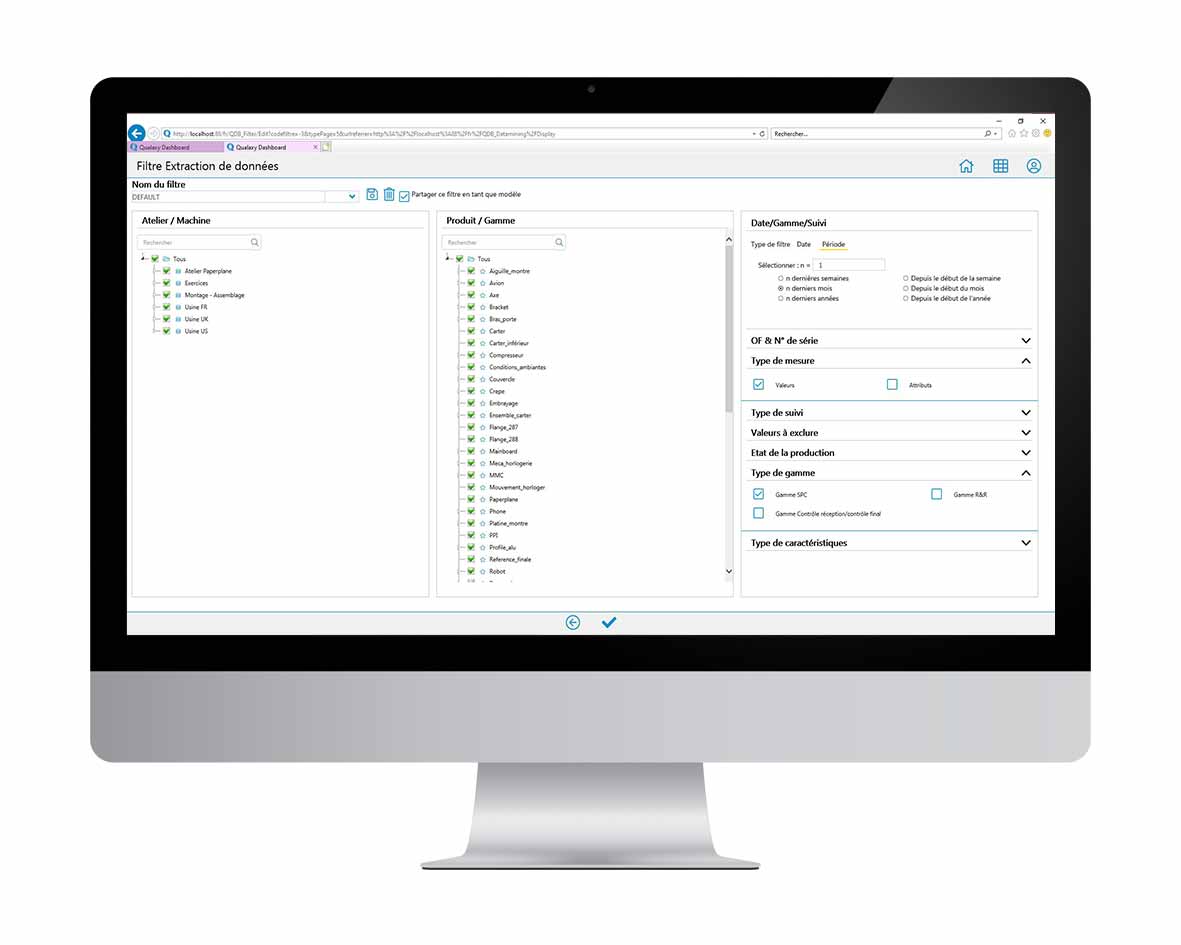
2/ Sector requirements
Depending on your sector of activity, you may be subject to specific regulatory standards:
– Aeronautics : AS/EN9100, NADCAP.
– Automotive: CNOMO, ISO TS, ISO TS 16949, MSA
– Medical : FDA CFR part 11
– Clockwork: ISO 2859 and 3951 Reception control (progressive control)
– etc.
Our MES conforms with many Quality standards but you can also set up your own internal company requirements
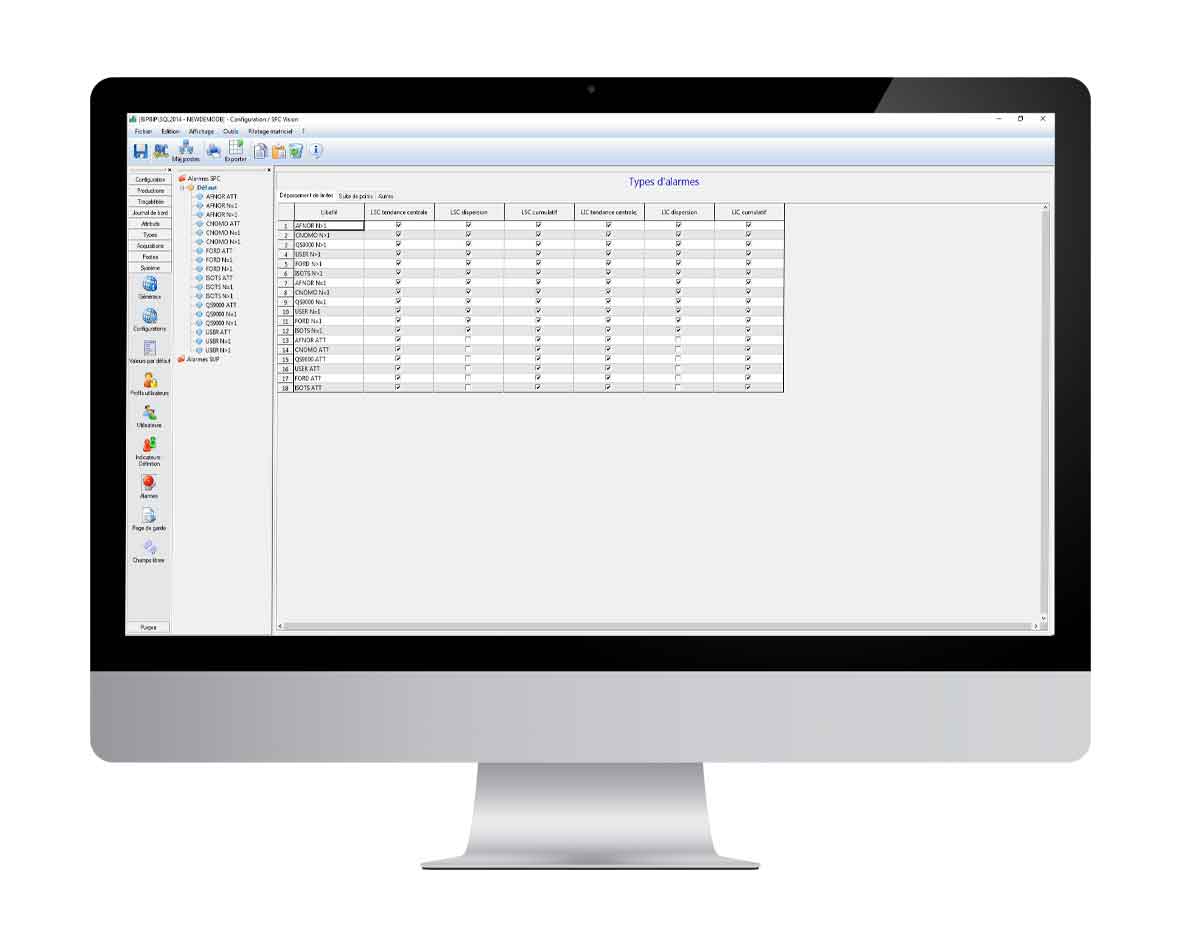
3/ Process revision and release control
It is obviously essential to be able to keep track of changes in the manufacturing and control procedures. Our system provides full configuration traceability for modifications including the ability to define multi-step version release processes.
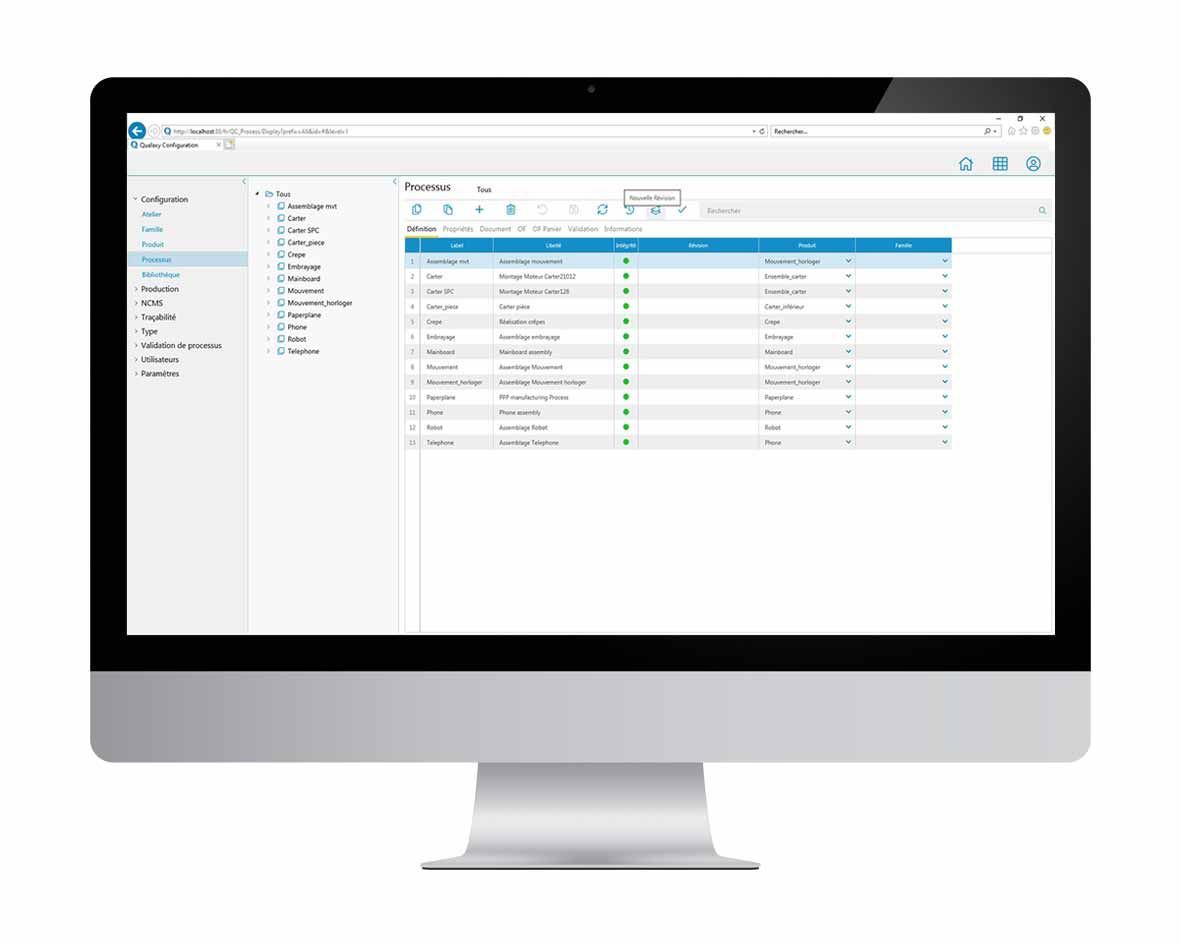
Not to be forgotten
It is therefore essential to choose a solution that natively integrates all of these sector requirements, but also the ability to set up in-house standards to meet your company needs.
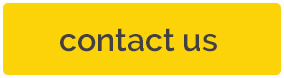
Total traceability
Every piece of information entered is recorded: you are sure to know who did what, when, where and how.
Quality standards
Our system meets many quality and regulatory requirements but you can also set up your own company standards.
"What version of the process was this?"
This question no longer needs to be asked: you keep a record all changes made to your processes.

Learn more
Data traceability: beyond customer requirements
Depending on your business challenges, keeping track of the information associated with the manufacturing orders carried out in your workshop makes it easy to find all the parts that share the same defects, and simplifies the detection of the root causes in order to take the appropriate corrective measures.
1/ Who? What? When? Where?
Full traceability of the production process makes it possible to know exactly the operator(s) involved in the manufacturing process, the nature of the operations carried out, as well as the date and the industrial means used.
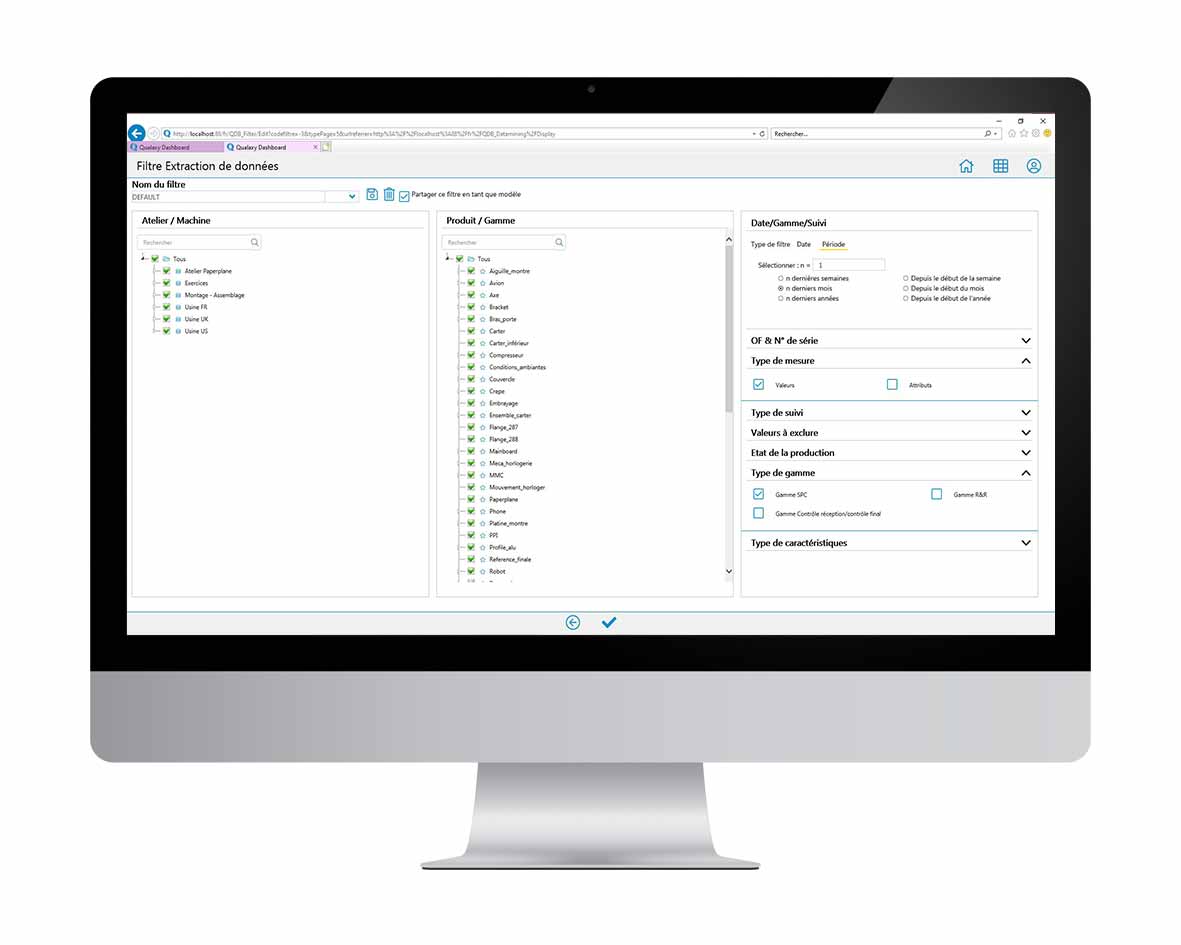
2/ Sector requirements
Depending on your sector of activity, you may be subject to specific regulatory standards:
– Aeronautics : AS/EN9100, NADCAP.
– Automotive: CNOMO, ISO TS, ISO TS 16949, MSA
– Medical : FDA CFR part 11
– Clockwork: ISO 2859 and 3951 Reception control (progressive control)
– etc.
Our MES conforms with many Quality standards but you can also set up your own internal company requirements
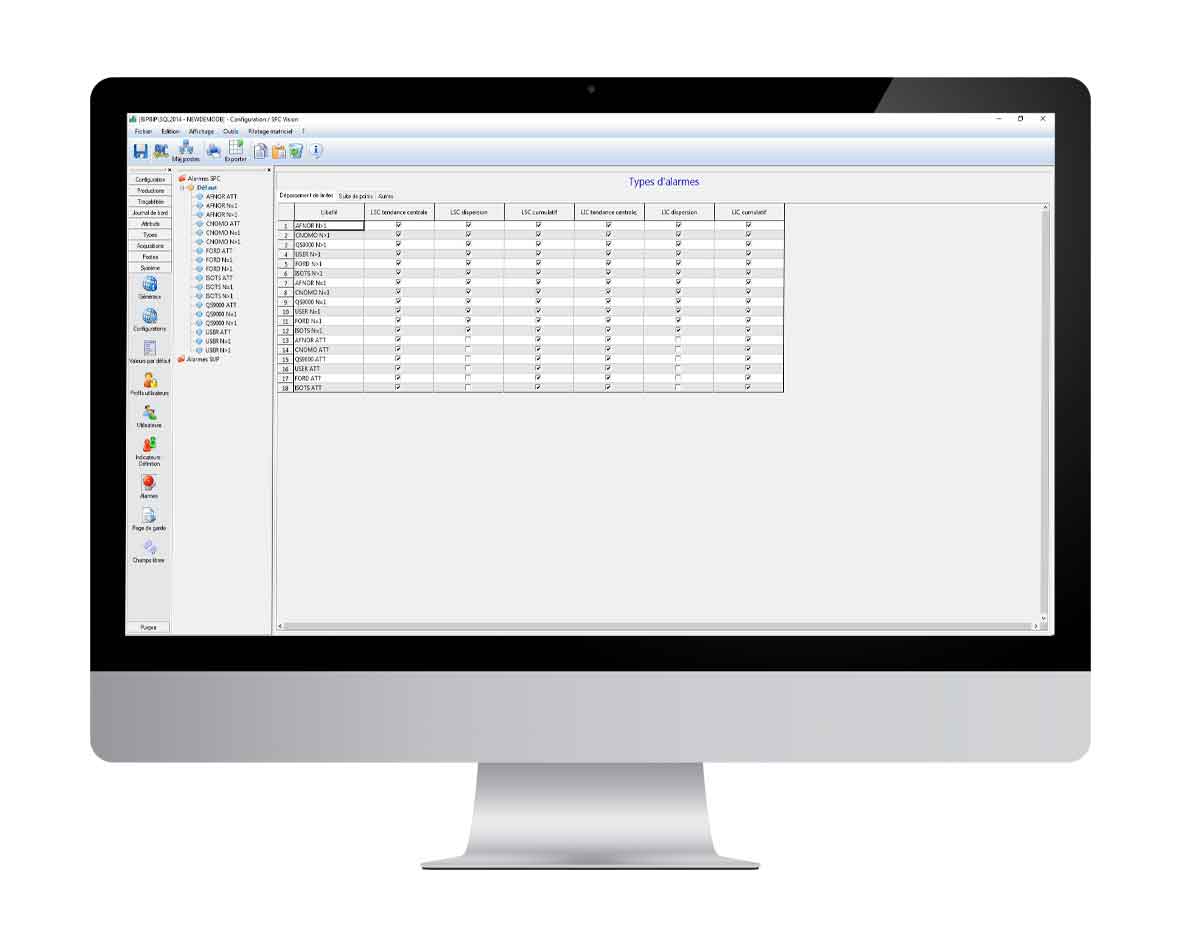
3/ Process revision and release control
It is obviously essential to be able to keep track of changes in the manufacturing and control procedures. Our system provides full configuration traceability for modifications including the ability to define multi-step version release processes.
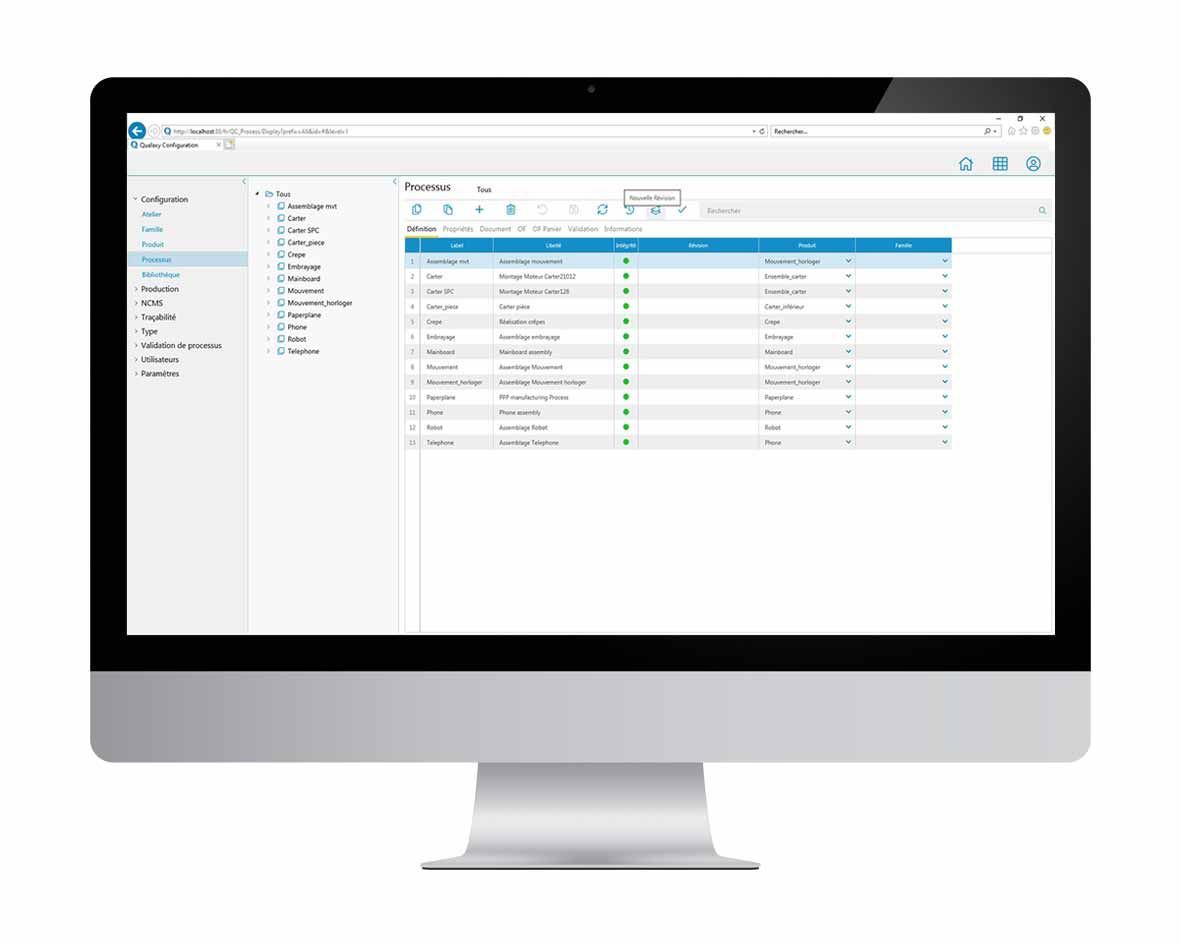
Not to be forgotten
It is therefore essential to choose a solution that natively integrates all of these sector requirements, but also the ability to set up in-house standards to meet your company needs.
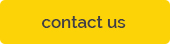
Paperless workshop
And therefore zero constraints! Your operators are finally guided by interactive work instructions.
A ready-to-use MES
Reliable, robust and fully configurable solution: no development is required, whatever your activity.
The work is made easier
Whether it’s on a tablet, PC or smartphone, the information is clear and personalised.
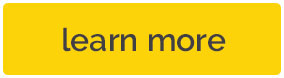
Learn more
Deploying an MES is half the job but it needs to be accepted by the shopfloor.
Winning the support of the teams.
Challenging existing work habits is not insignificant. Indeed, you bring a dose of the unknown, and therefore risk. To limit as much as possible the rejection linked to this risk-taking, it is necessary to answer two questions: « what is the source of the needs expressed by my teams? « and « what will make the proposed solution meet their expectations? »
1/ Simplify the work of the operators
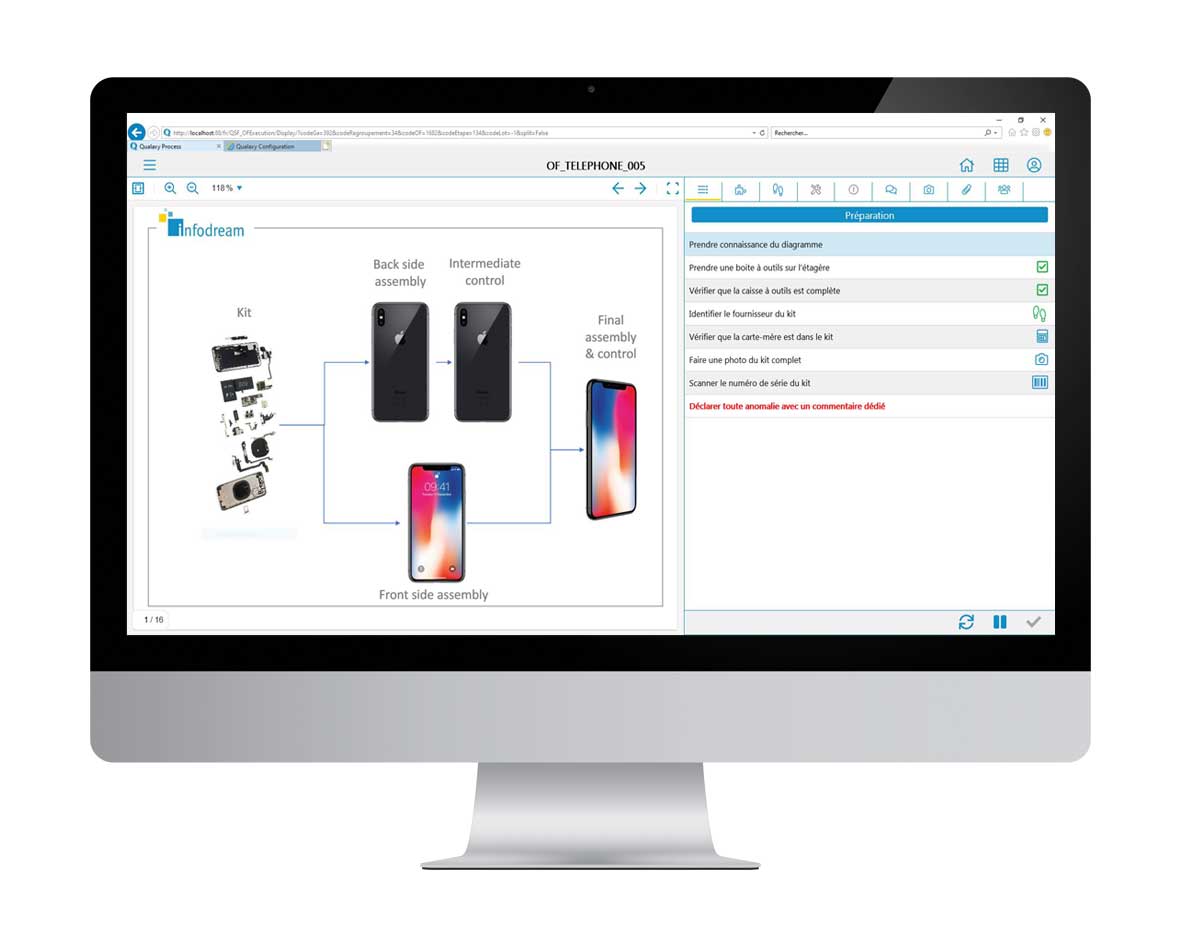
The primary purpose of MES-type tools is to allow your operators to concentrate on their know-how, providing them with the information they need, when they need it. In addition, these tools automate the transfer of information: no more writing or paper handling, the tool takes care of everything.
2/ Fluid communication between teams
The MES is similar to an information exchange platform between the ERP and the workshop. Thus, its main interest is to share data between the different manufacturing stations, but also with all the company’s departments for whom the progress of the work orders is key information (logistics, invoicing, etc.).
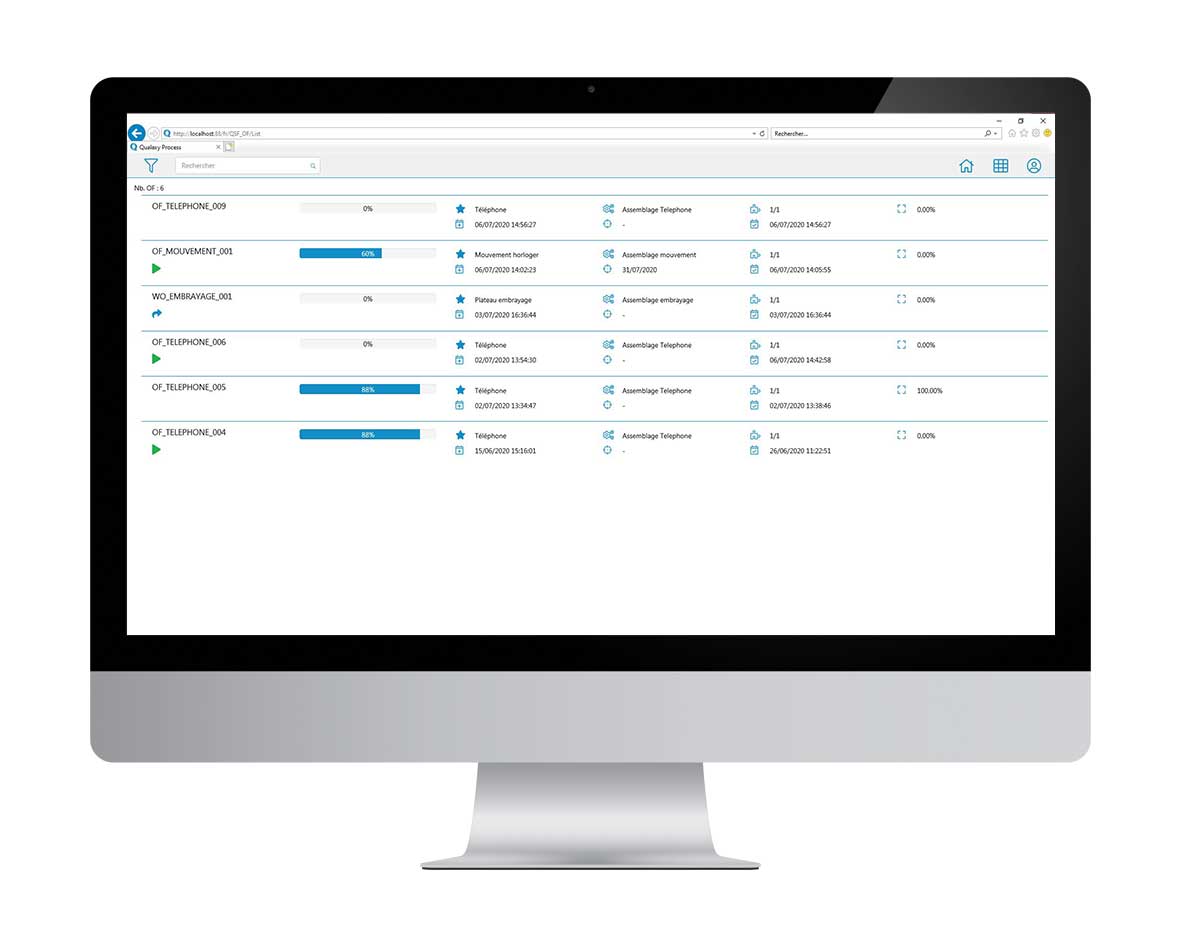
3/ A tool that is easy to use
Among the key factors in the acceptance of IT solutions are the ergonomics of the software, the fluidity of multi-support use (pc/tablet/smartphones) in an industrial environment, and the possibility of customisation according to the specificities linked to the missions of the user.
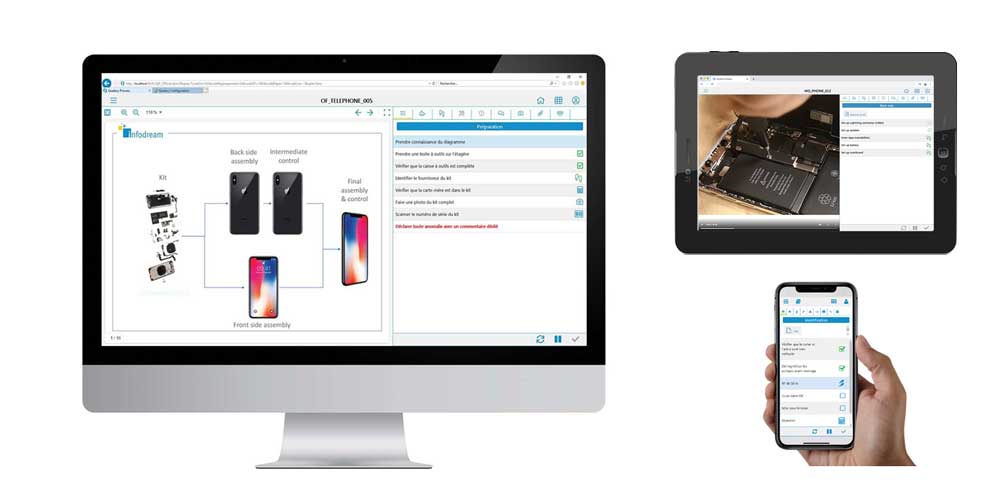
Not to be forgotten
To ensure successful change management in a project of this scale, it is advisable to think in deploymen stages: POC > pilot project > deployment by successive perimeters. In this way, it is possible to gradually understand the levers to be implemented to successfully deploy the chosen tool.
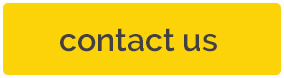
Paperless workshop
And therefore zero constraints! Your operators are finally guided by interactive work instructions.
A ready-to-use MES
Reliable, robust and fully configurable solution: no development is required, whatever your activity.
The work is made easier
Whether it’s on a tablet, PC or smartphone, the information is clear and personalised.

Learn more
Deploying an MES is half the job but it needs to be accepted by the shopfloor.
Winning the support of the teams.
Challenging existing work habits is not insignificant. Indeed, you bring a dose of the unknown, and therefore risk. To limit as much as possible the rejection linked to this risk-taking, it is necessary to answer two questions: « what is the source of the needs expressed by my teams? « and « what will make the proposed solution meet their expectations? »
1/ Simplify the work of the operators
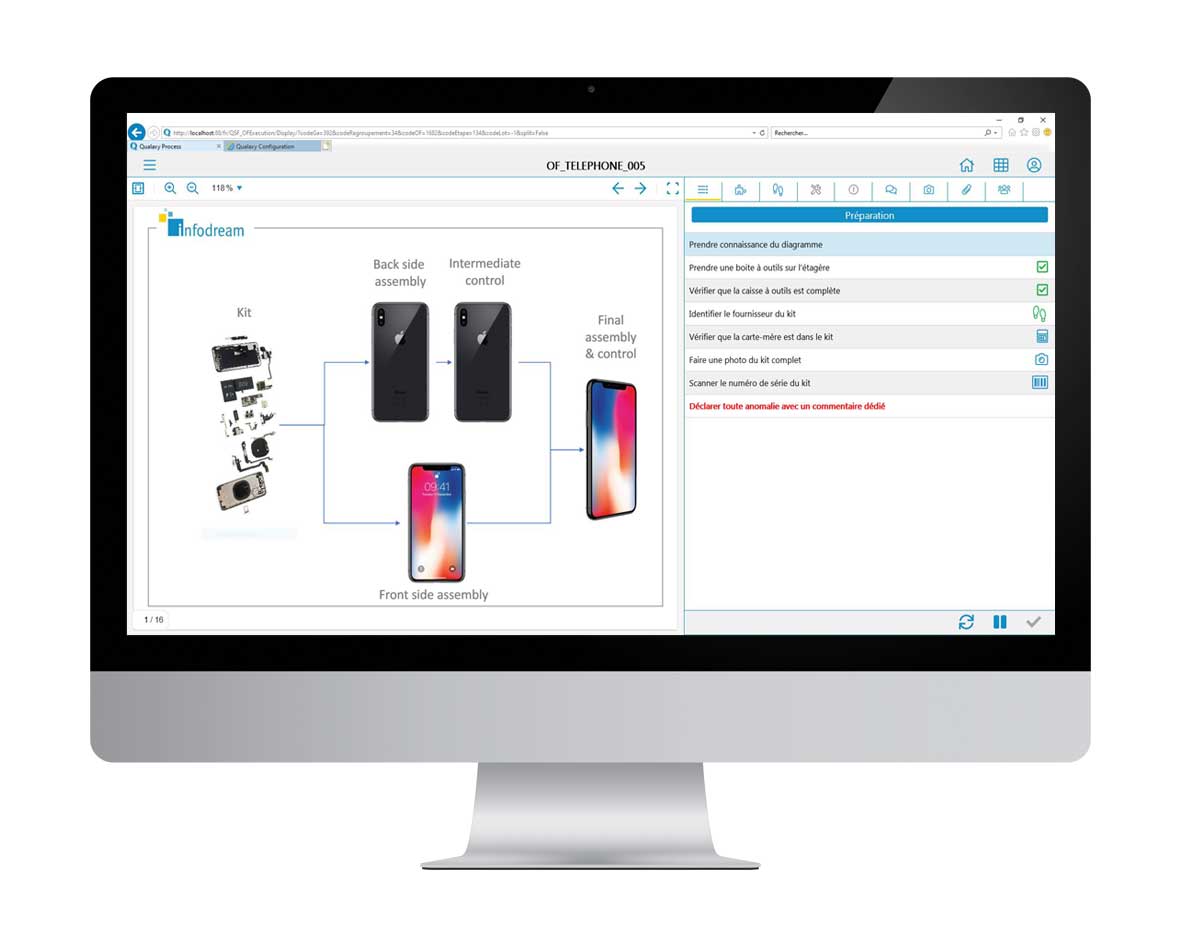
The primary purpose of MES-type tools is to allow your operators to concentrate on their know-how, providing them with the information they need, when they need it. In addition, these tools automate the transfer of information: no more writing or paper handling, the tool takes care of everything.
2/ Fluid communication between teams
The MES is similar to an information exchange platform between the ERP and the workshop. Thus, its main interest is to share data between the different manufacturing stations, but also with all the company’s departments for whom the progress of the work orders is key information (logistics, invoicing, etc.).
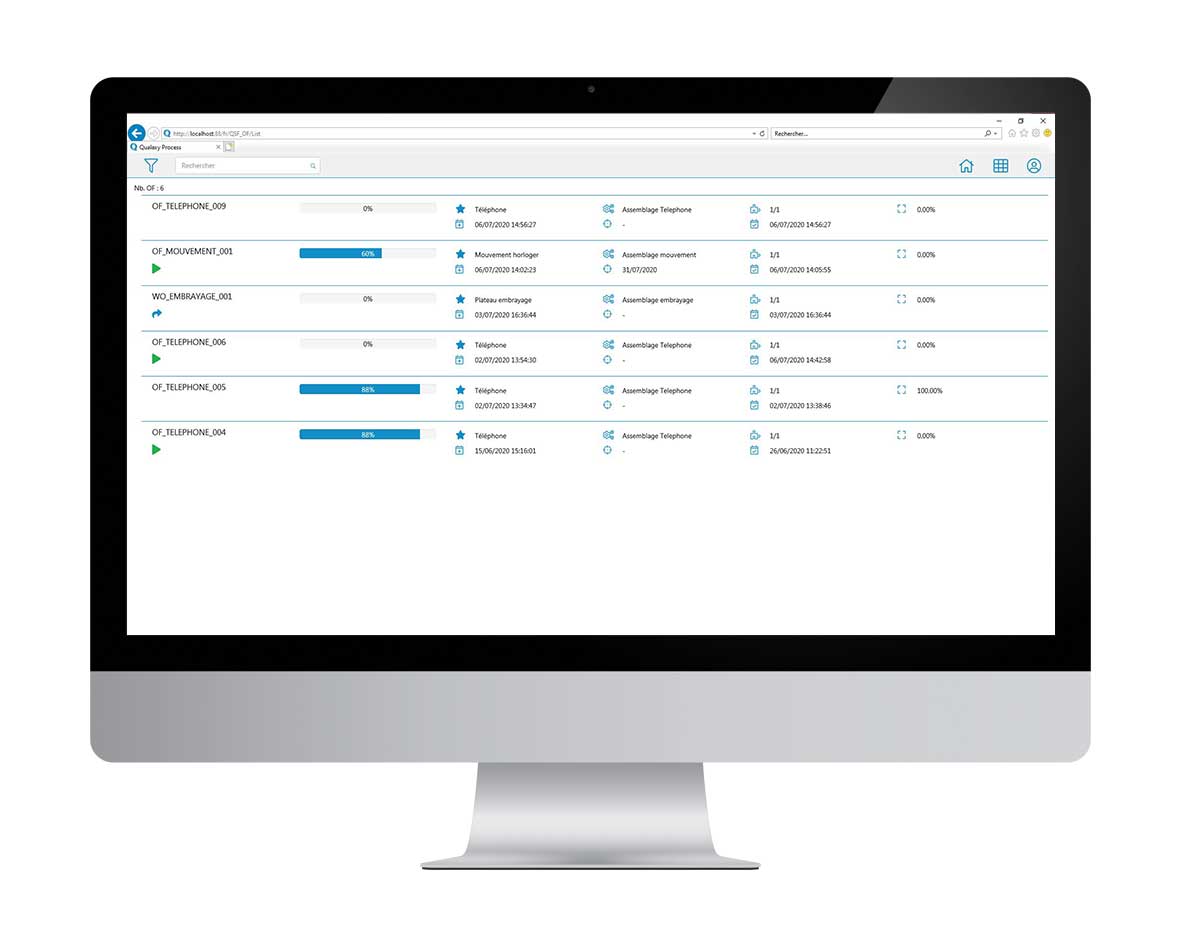
3/ A tool that is easy to use
Among the key factors in the acceptance of IT solutions are the ergonomics of the software, the fluidity of multi-support use (pc/tablet/smartphones) in an industrial environment, and the possibility of customisation according to the specificities linked to the missions of the user.
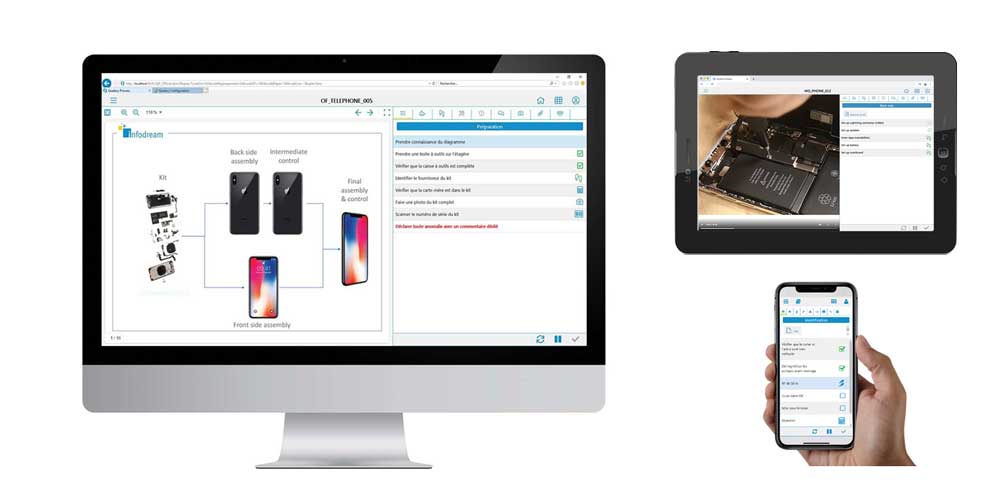
Not to be forgotten
To ensure successful change management in a project of this scale, it is advisable to think in deploymen stages: POC > pilot project > deployment by successive perimeters. In this way, it is possible to gradually understand the levers to be implemented to successfully deploy the chosen tool.
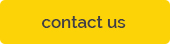
Anticipating Quality
With SPC monitoring, detect in real time the progressive drifts of your productions before the appearance of non-conformities.
Supplier quality: the phantom threat
Your incoming controls are optimised: a real barrier against imported non-compliance!
360 ° control
In one click, visualise your KPIs and the performance of your workshop.
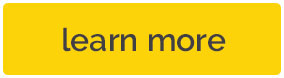
Learn more
Continuous improvement: tools for better management
Continuous improvement: must have & toolbox.
In such a competitive world, it is essential to give yourself the means to produce better, faster and cheaper than your competitors. Continuous improvement is a relevant lever of action in this sense, but must be a permanent, omnipresent and structured approach in order to improve the efficiency of your company’s processes on a daily basis for the satisfaction of your customers.
1/ Control your processes
Acceptance or rejection of supplier batches, AQL management, real-time quality control… Stop being subjected to your processes by intervening as a reactive measure, but take the lead by correcting production drifts in advance.
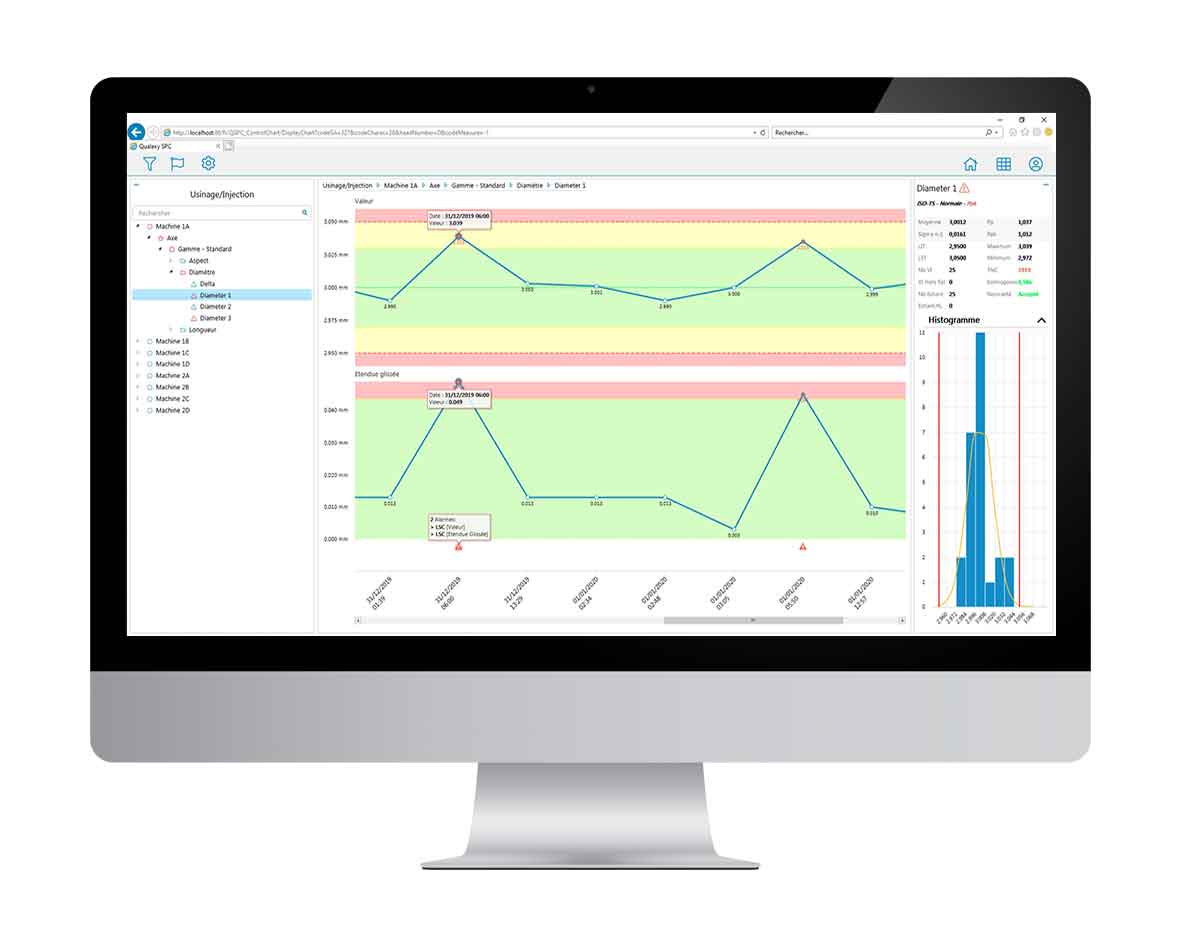
2/ Optimise the costs linked to quality control
Controlling has a cost. This cost is acceptable if it allows the company to improve the quality of its industrial process. It is not acceptable if it is useless and inefficient. Any relevant continuous improvement approach must therefore include the search for optimisation of the load and quality of the controls carried out.
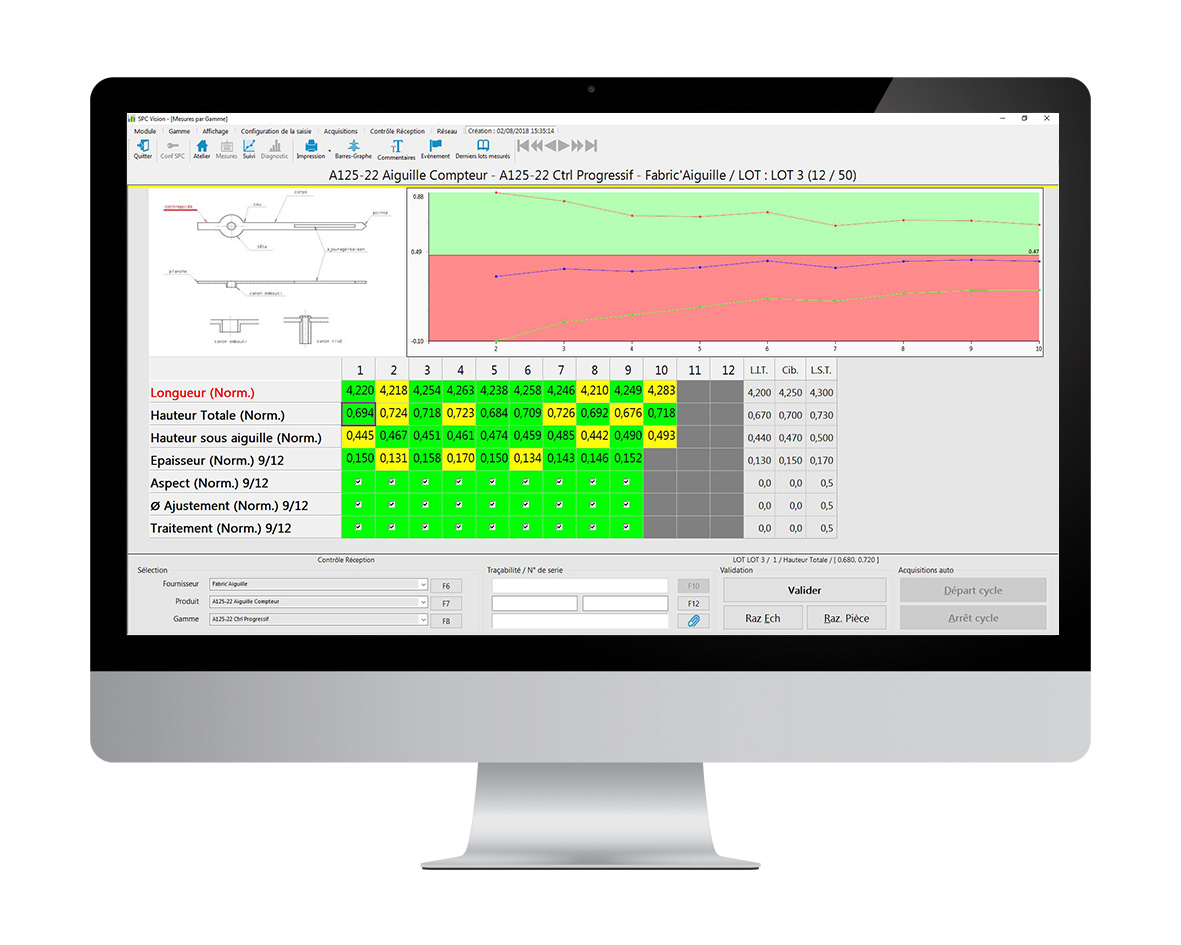
3/ Steering: decision support tools
To enable you to make the right decisions, you need clear quality and performance indicators. Visualisation of alarms, changes in the capability of your machines or the times that make up your manufacturing processes are essential data for a lean analysis of your business.
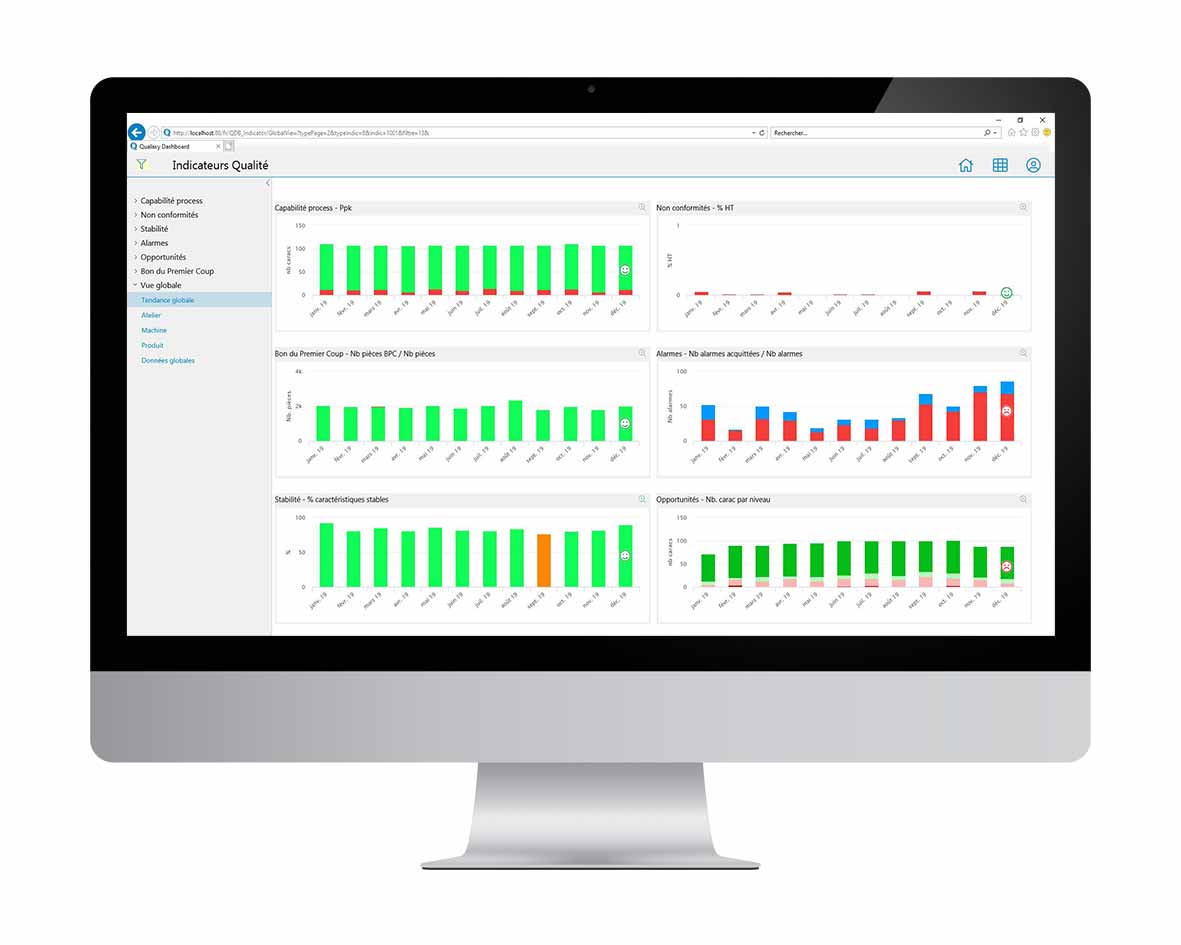
Not to be forgotten
Monitoring an industrial activity involves several levels of analysis: instantaneous, medium and long term. Therefore, it is important to deploy a tool offering these complementary angles of analysis.
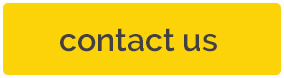
Anticipating Quality
With SPC monitoring, detect in real time the progressive drifts of your productions before the appearance of non-conformities.
Supplier quality: the phantom threat
Your incoming controls are optimised: a real barrier against imported non-compliance!
360 ° control
In one click, visualise your KPIs and the performance of your workshop.

Learn more
Continuous improvement: tools for better management
Continuous improvement: must have & toolbox.
In such a competitive world, it is essential to give yourself the means to produce better, faster and cheaper than your competitors. Continuous improvement is a relevant lever of action in this sense, but must be a permanent, omnipresent and structured approach in order to improve the efficiency of your company’s processes on a daily basis for the satisfaction of your customers.
1/ Control your processes
Acceptance or rejection of supplier batches, AQL management, real-time quality control… Stop being subjected to your processes by intervening as a reactive measure, but take the lead by correcting production drifts in advance.
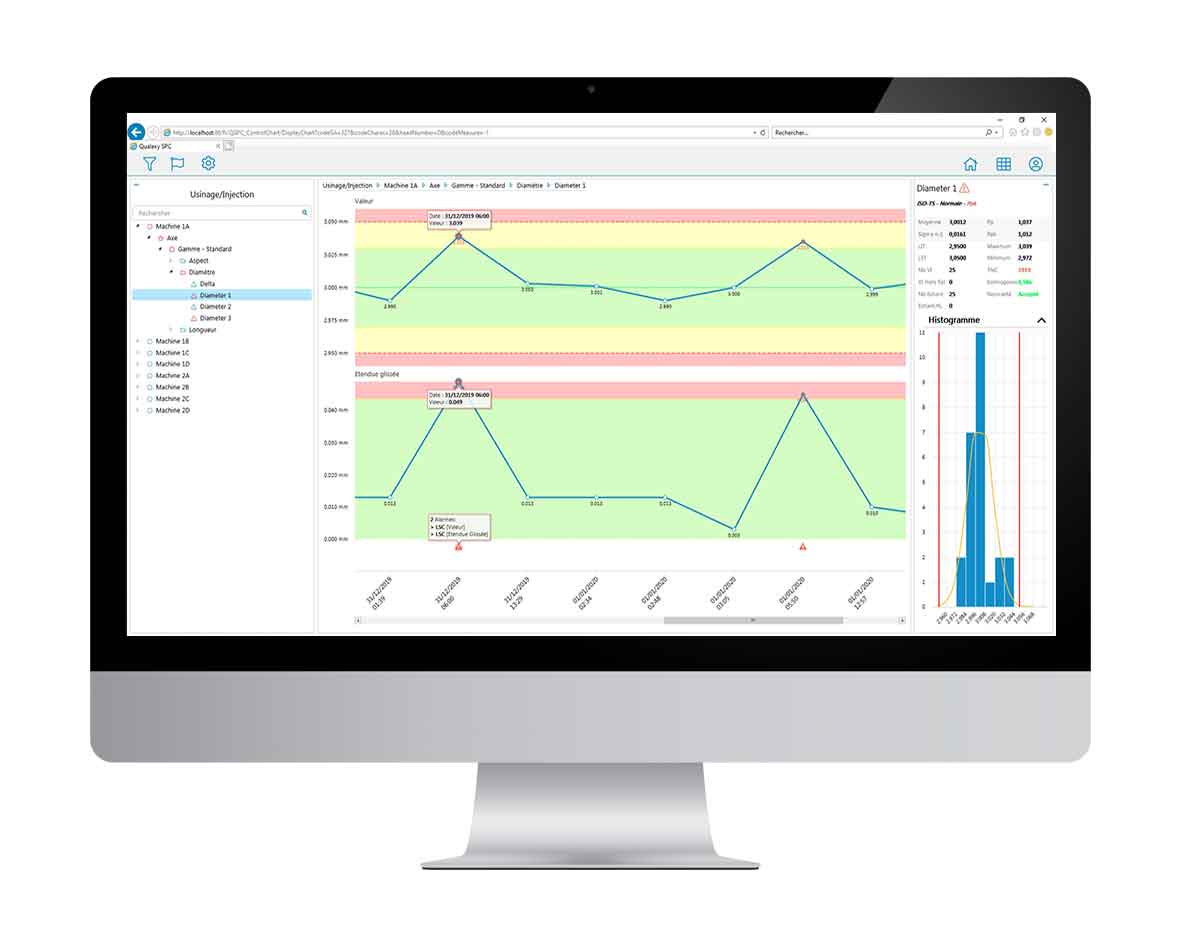
2/ Optimise the costs linked to quality control
Controlling has a cost. This cost is acceptable if it allows the company to improve the quality of its industrial process. It is not acceptable if it is useless and inefficient. Any relevant continuous improvement approach must therefore include the search for optimisation of the load and quality of the controls carried out.
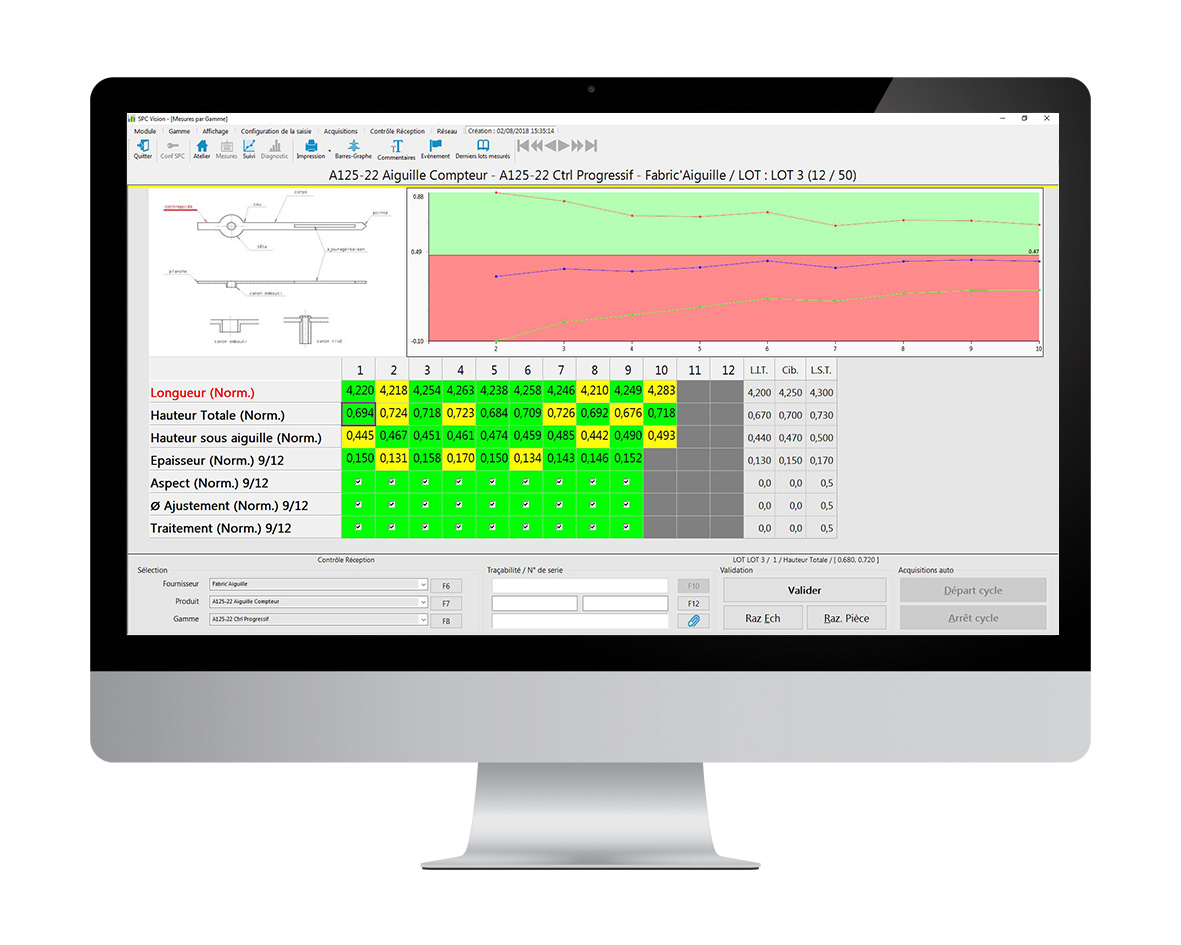
3/ Steering: decision support tools
To enable you to make the right decisions, you need clear quality and performance indicators. Visualisation of alarms, changes in the capability of your machines or the times that make up your manufacturing processes are essential data for a lean analysis of your business.
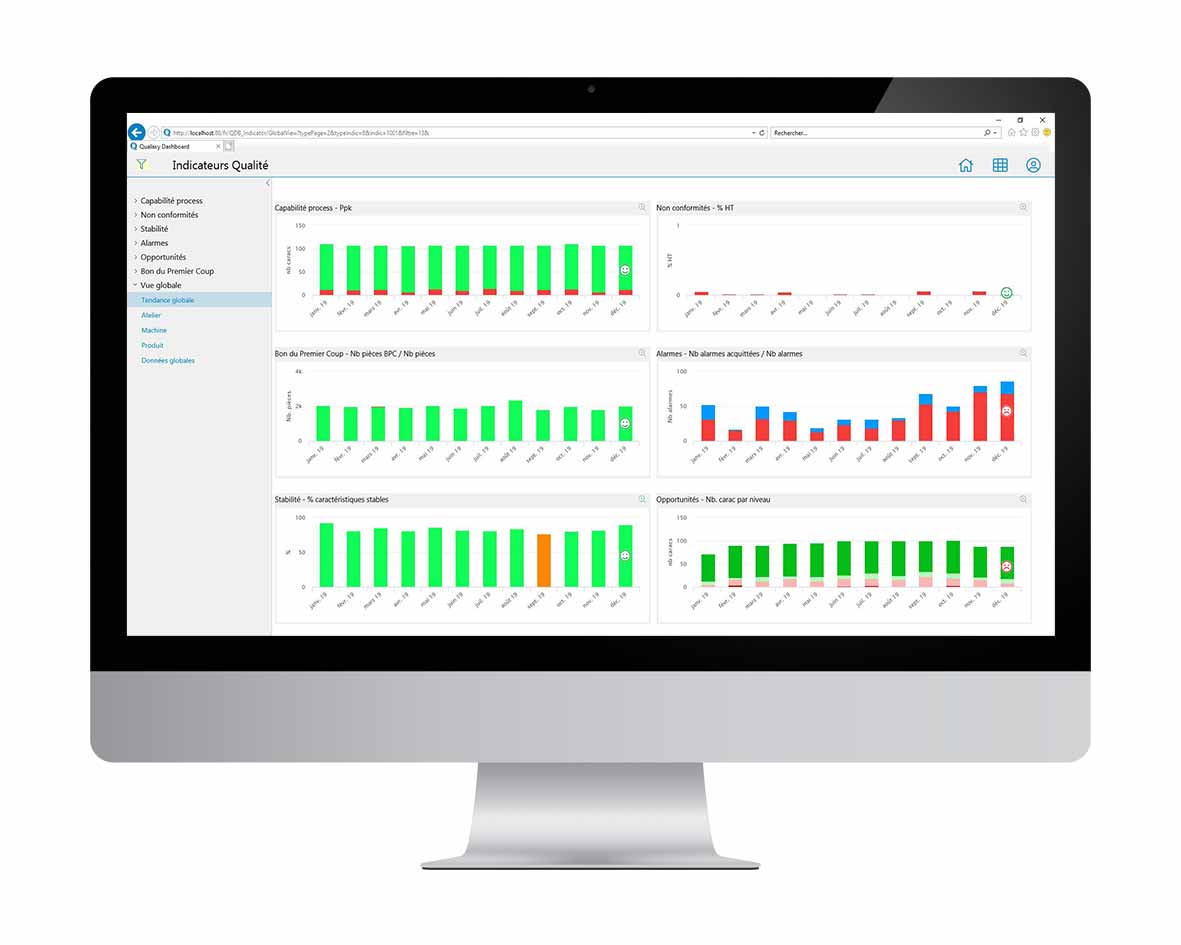
Not to be forgotten
Monitoring an industrial activity involves several levels of analysis: instantaneous, medium and long term. Therefore, it is important to deploy a tool offering these complementary angles of analysis.
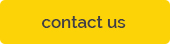
Supplier quality: the phantom threat
Your incoming controls are optimised: a real barrier against imported non-compliance!
360 ° control
In one click, visualise your KPIs and the performance of your workshop.
Save time, of course.
Who can afford to waste time controlling what is not necessary?
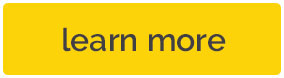
Learn more
Optimise quality control costs
Controlling has a cost. This is acceptable if and only if it allows the company to improve the quality of its industrial process. It is not acceptable if it is useless and inefficient. Any relevant continuous improvement approach must therefore include the search for optimisation of the load and quality of the controls carried out.
1/ Time is money
You know this better than anyone else: carrying out control operations takes time; time which is all the more precious in a permanent process of optimisation.
2/ Reducing costs, yes. But not at the price of quality.
Optimising inspection activities must always maintain the quality objectives set. It is up to MES-type tools to guarantee the success of this approach: the notion of « quality steering » takes on its full meaning here.
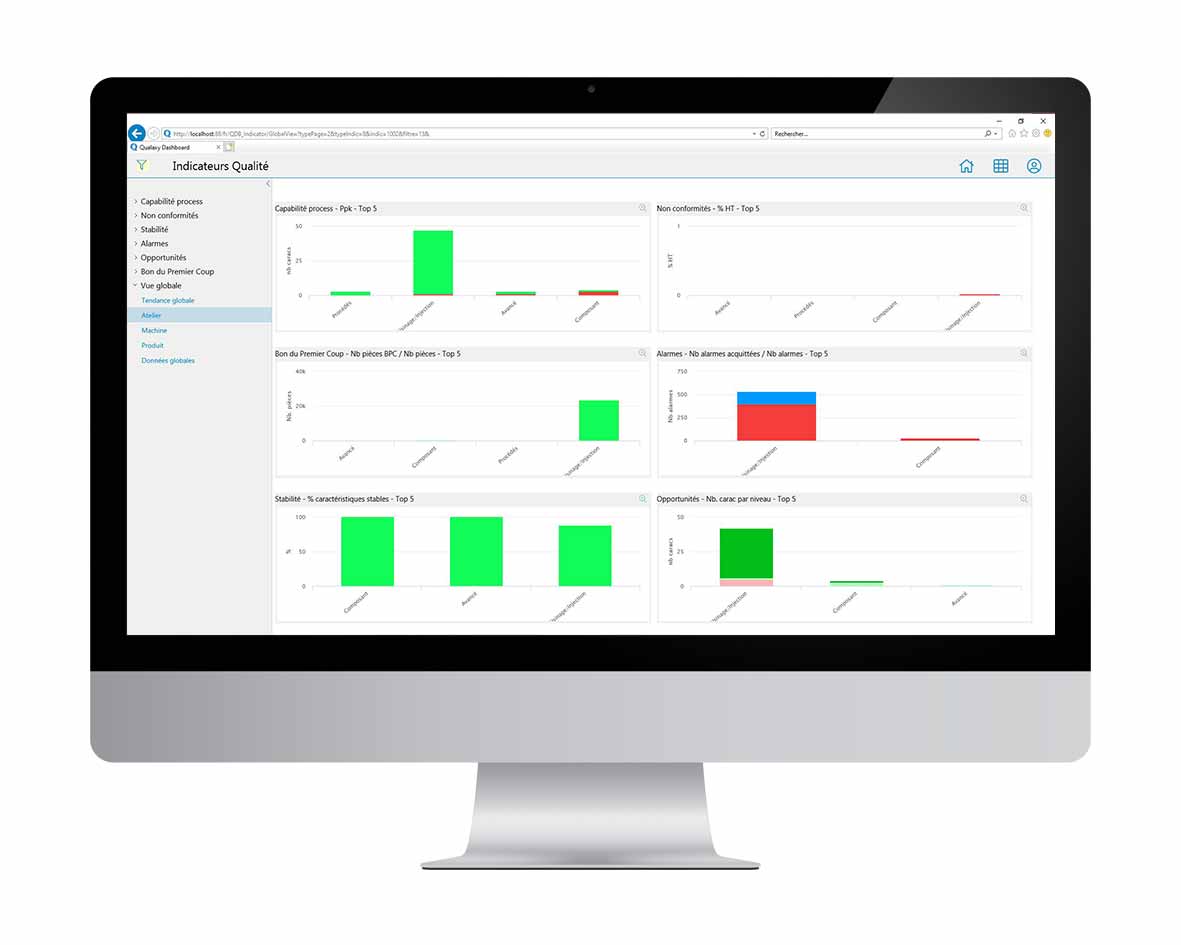
3/ Detect opportunities to reduce inspection
Depending on the quality indicators relevant to your organisation (Cp/Cpk, Pp/Ppk,…), you should be able to determine your optimisation strategy. On the basis of clear and reliable tools, you will be able to identify possible areas to reduce inspection, without compromising the quality levels.
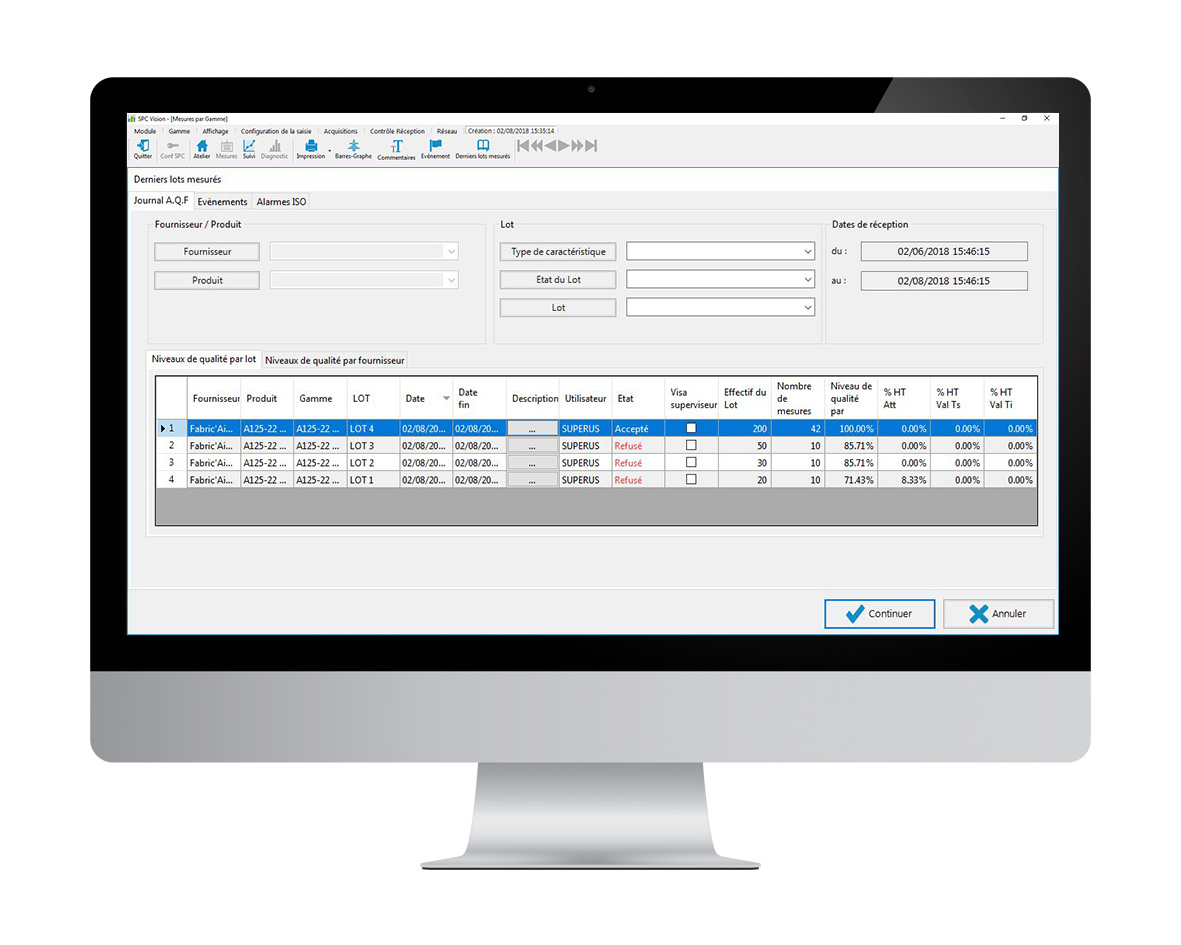
Not to be forgotten
There are many tools available to articulate an optimal quality control approach: modulation, standards, dynamisation, etc.
It is important to integrate these reflections into the strategy to be deployed in order to determine the tool best suited to meet the needs expressed.
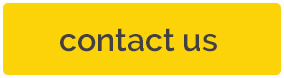
Supplier quality: the phantom threat
Your incoming controls are optimised: a real barrier against imported non-compliance!
360 ° control
In one click, visualise your KPIs and the performance of your workshop.
Save time, of course.
Who can afford to waste time controlling what is not necessary?

Learn more
Optimise quality control costs
Controlling has a cost. This is acceptable if and only if it allows the company to improve the quality of its industrial process. It is not acceptable if it is useless and inefficient. Any relevant continuous improvement approach must therefore include the search for optimisation of the load and quality of the controls carried out.
1/ Time is money
You know this better than anyone else: carrying out control operations takes time; time which is all the more precious in a permanent process of optimisation.
2/ Reducing costs, yes. But not at the price of quality.
Optimising inspection activities must always maintain the quality objectives set. It is up to MES-type tools to guarantee the success of this approach: the notion of « quality steering » takes on its full meaning here.
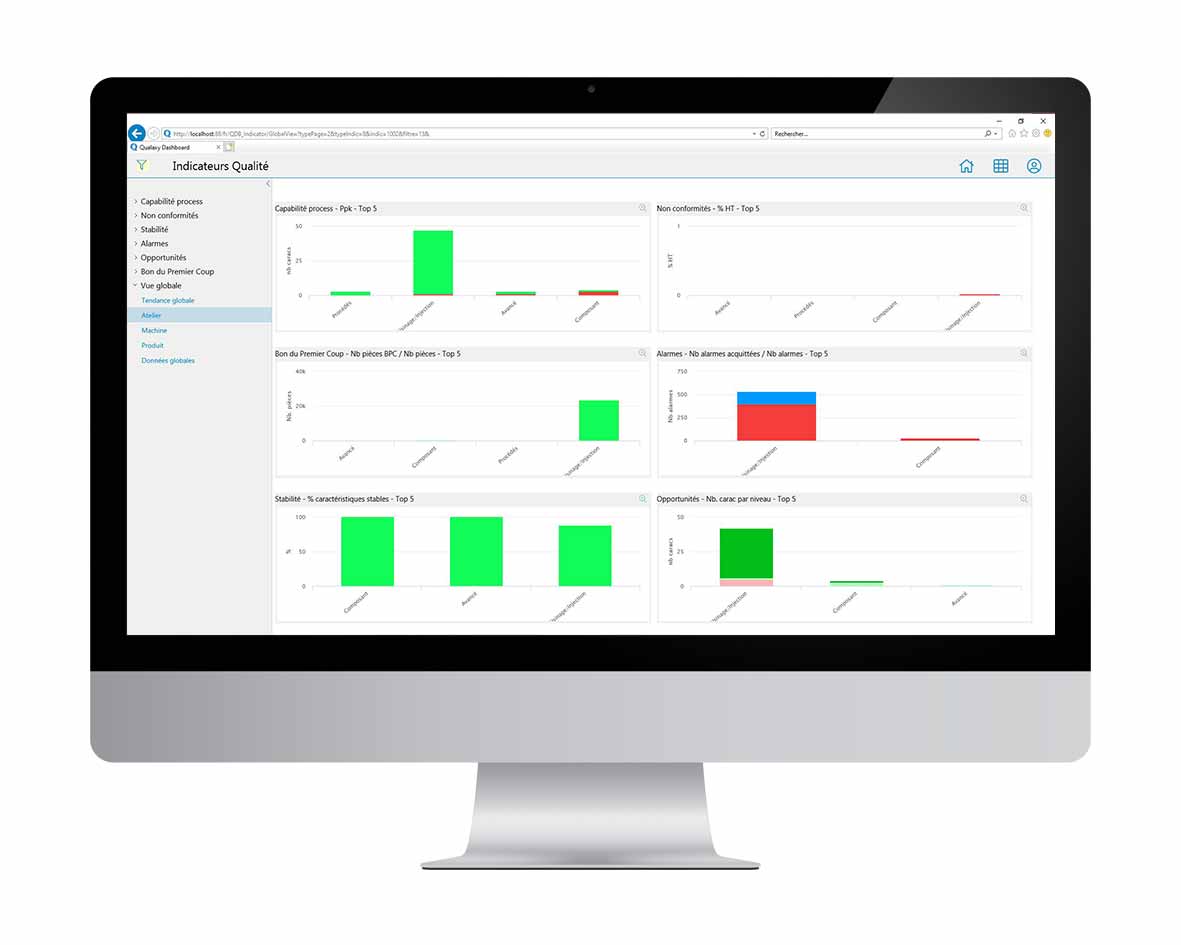
3/ Detect opportunities to reduce inspection
Depending on the quality indicators relevant to your organisation (Cp/Cpk, Pp/Ppk,…), you should be able to determine your optimisation strategy. On the basis of clear and reliable tools, you will be able to identify possible areas to reduce inspection, without compromising the quality levels.
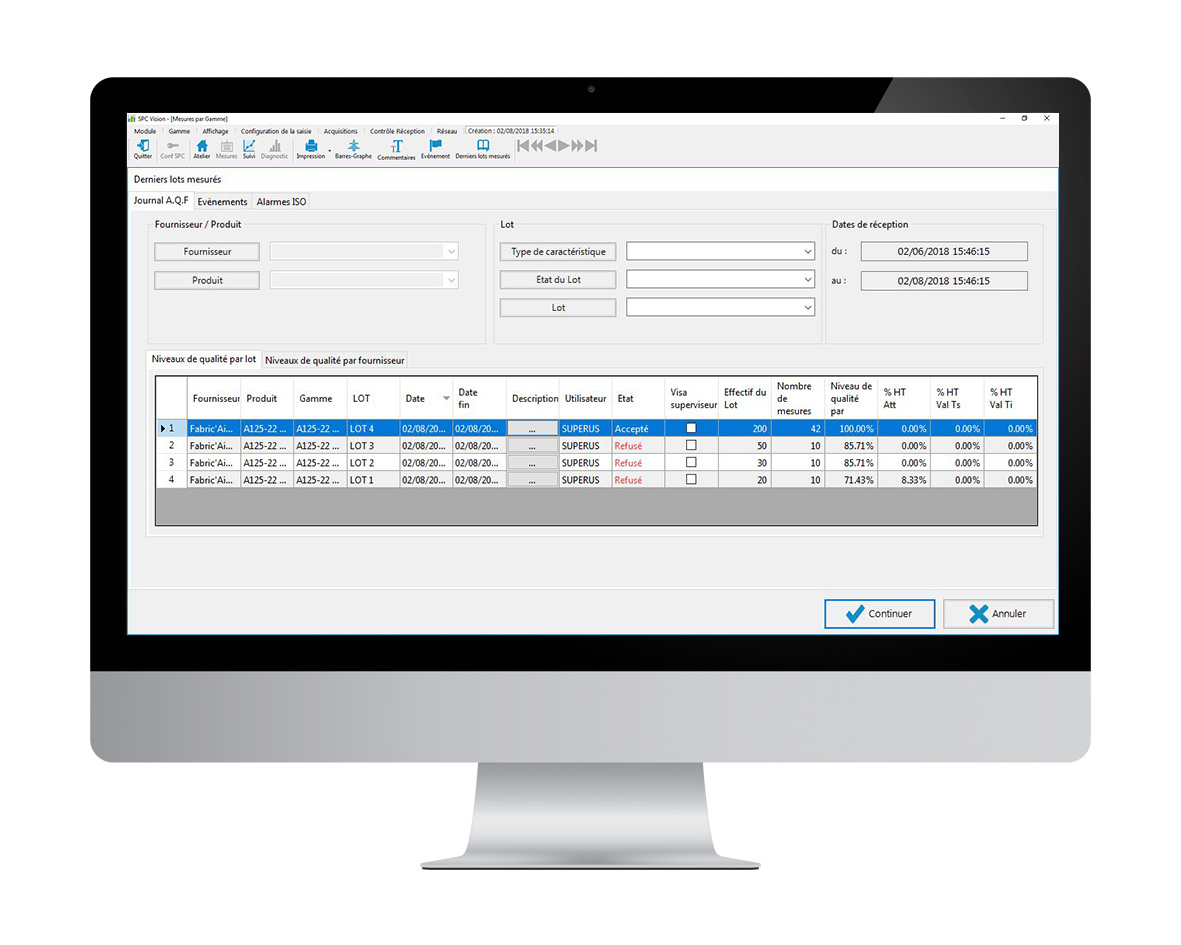
Not to be forgotten
There are many tools available to articulate an optimal quality control approach: modulation, standards, dynamisation, etc.
It is important to integrate these reflections into the strategy to be deployed in order to determine the tool best suited to meet the needs expressed.
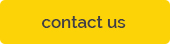
"What's the status of this WO?"
Instant response on the shop floor, progress synchronised in real time with your ERP. A real time-saver!
360 ° control
In one click, visualise your KPIs and the performance of your workshop.
Hidden costs: looking for lost time
With the traceability of time spent, you know the true cost of your production and your bottlenecks.
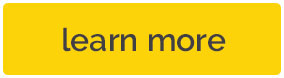
Learn more
1/ Shared data in real time
The digitisation of the controls and follow-up actions brings the undeniable advantage of making it possible to transfer data from the workshop in real time. No more e-mail exchanges, meetings or manual data entry: the data is available and only awaits your decisions.
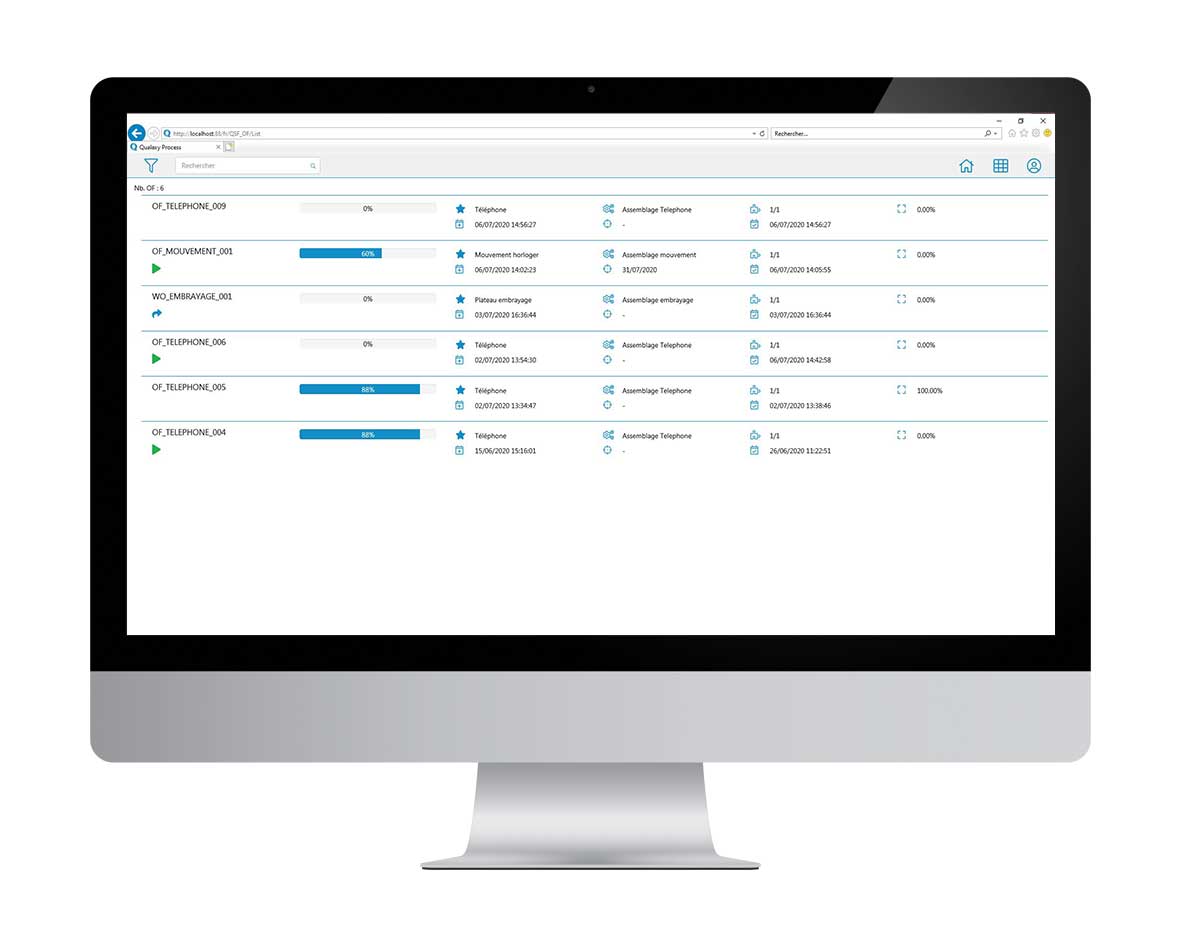
2/ Clear and organised information
The ergonomics of the quality indicators is a key factor in user acceptance. Their layout, use or visual appearance must enable important information to be captured immediately.
3/ Personalisation to the user
It is essential to provide for the possibility of parameterising the display of relevant information at user level.
In fact, depending on its topicality, the relevant indicators may need to evolve.
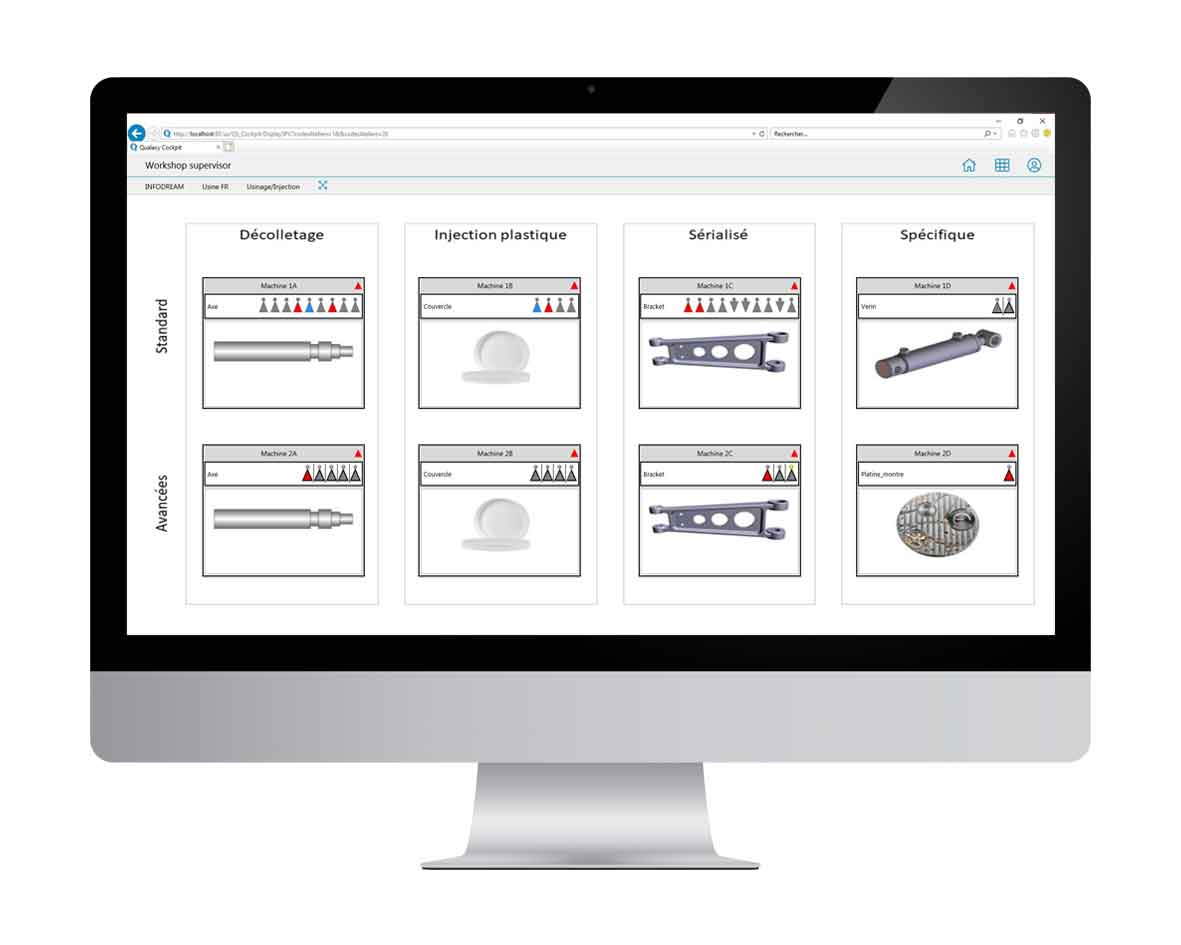
Not to be forgotten
The digitalisation of manufacturing processes and associated controls implies a real reflection on the use of the most suitable support: smartphone, tablet, screen…
If many tools can be used in the workshop, depending on the nature of the manufacturing processes, some will have to be preferred to provide real user comfort.
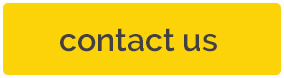
"What's the status of this WO?"
Instant response on the shop floor, progress synchronised in real time with your ERP. A real time-saver!
360 ° control
In one click, visualise your KPIs and the performance of your workshop.
Hidden costs: looking for lost time
With the traceability of time spent, you know the true cost of your production and your bottlenecks.

Learn more
1/ Shared data in real time
The digitisation of the controls and follow-up actions brings the undeniable advantage of making it possible to transfer data from the workshop in real time. No more e-mail exchanges, meetings or manual data entry: the data is available and only awaits your decisions.
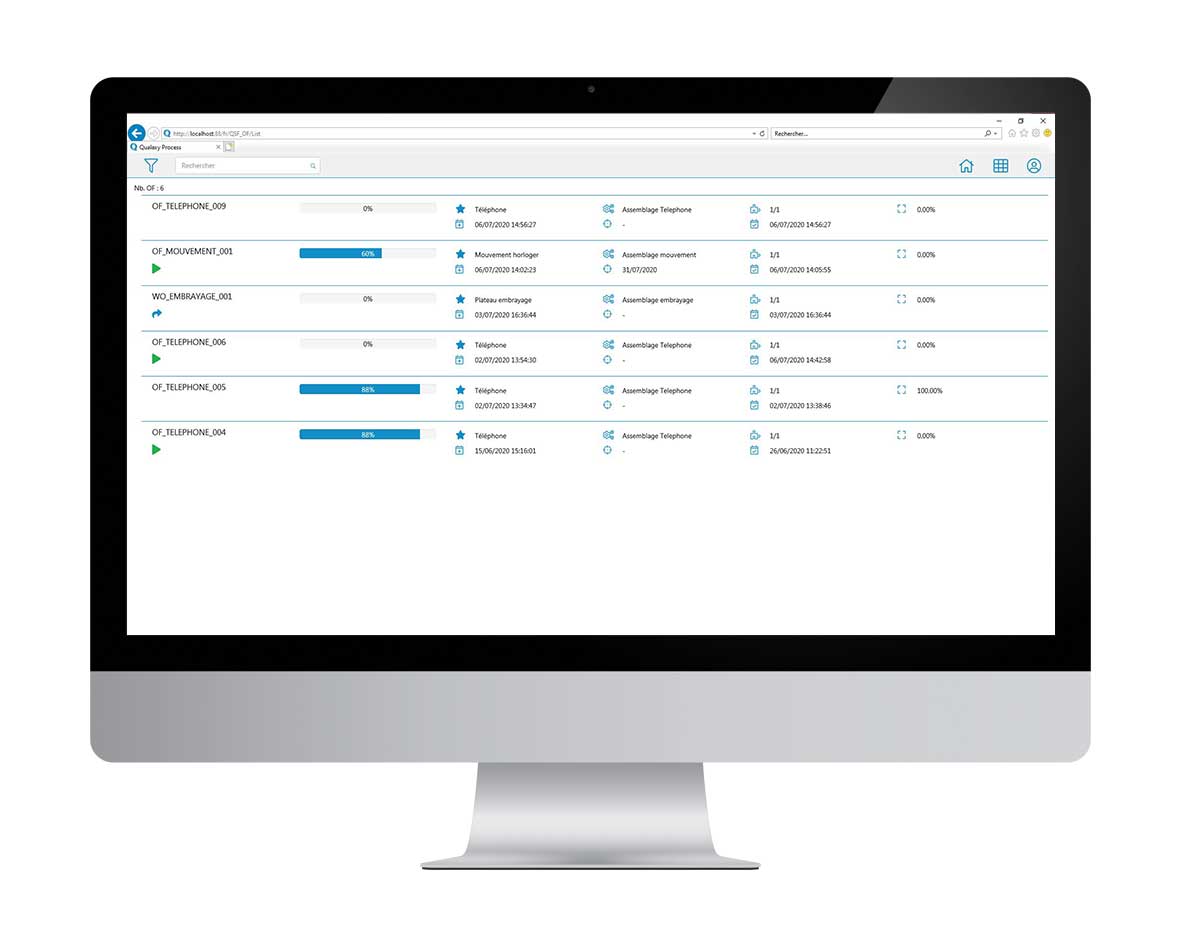
2/ Clear and organised information
The ergonomics of the quality indicators is a key factor in user acceptance. Their layout, use or visual appearance must enable important information to be captured immediately.
3/ Personalisation to the user
It is essential to provide for the possibility of parameterising the display of relevant information at user level.
In fact, depending on its topicality, the relevant indicators may need to evolve.
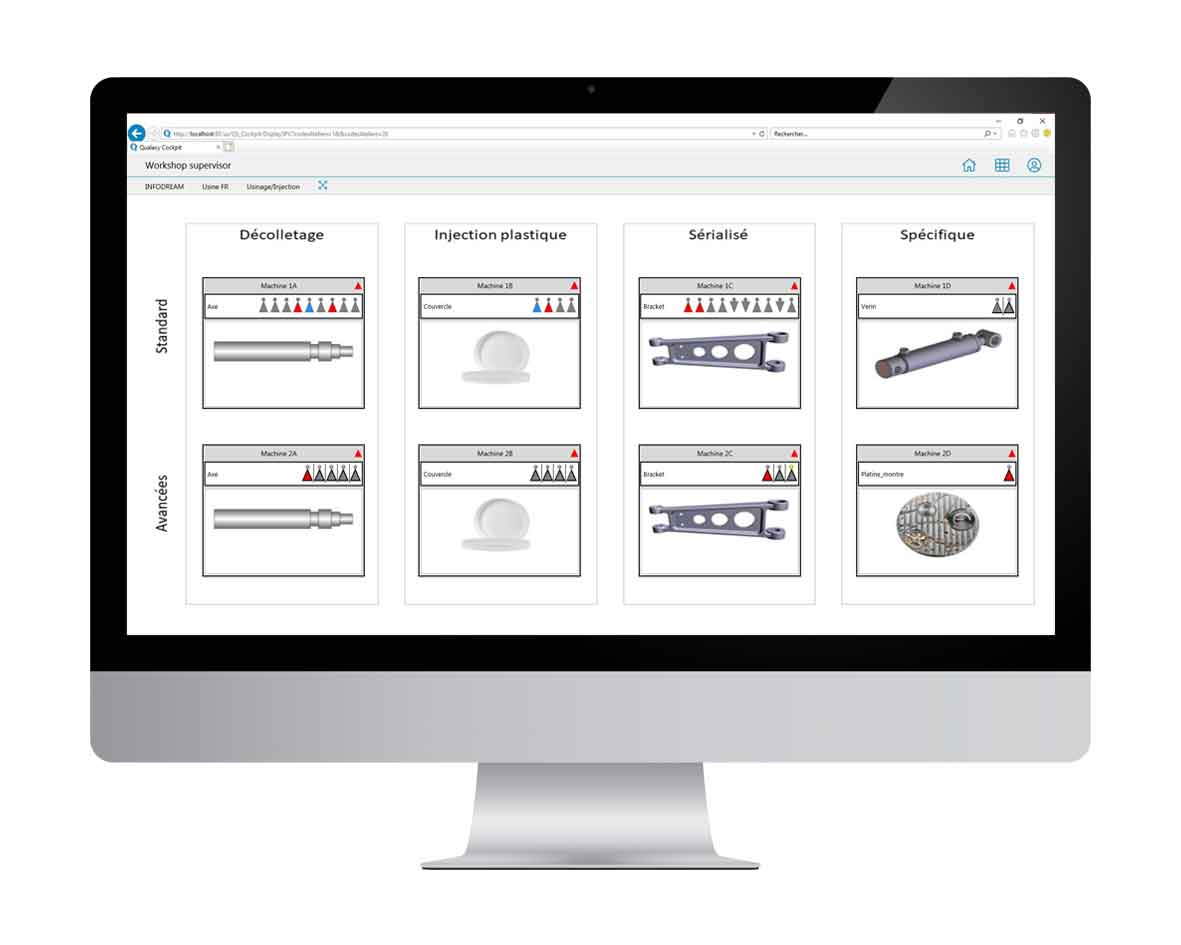
Not to be forgotten
The digitalisation of manufacturing processes and associated controls implies a real reflection on the use of the most suitable support: smartphone, tablet, screen…
If many tools can be used in the workshop, depending on the nature of the manufacturing processes, some will have to be preferred to provide real user comfort.
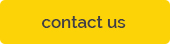