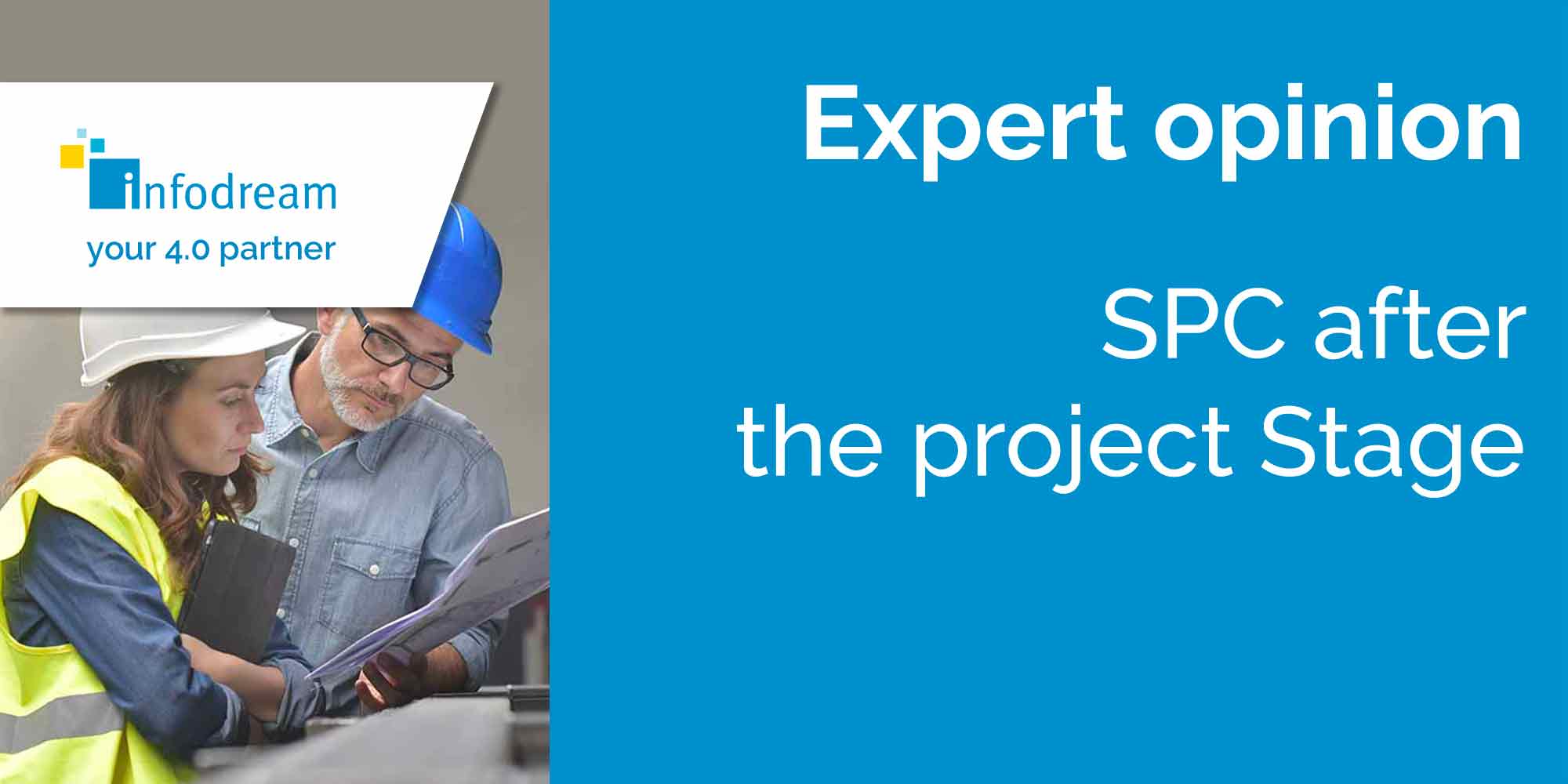
SPC after the « project » Stage
How and when to make the transition from the project mode of the SPC approach to its daily use? Who should take the baton? These questions arise for all types of project, but we have some answers for you.
Leading an SPC project is above all applying a project methodology, but it is also a continuous improvement approach and above all a change management.
It is a unifying project that brings together the Methods, Quality, Production, Design Office and General Management departments… It is therefore a structuring project for the company.
The success of this project requires involvement, means and resources.
Let’s assume that all the prerequisites have been met and that the project has been successfully completed. Who can be handed over after an SPC project?
SPC as a production tool
We find ourselves in a more general problem of perpetuating good practices in an industrial environment. The transition from project mode (with a project manager, actors and allocated resources) to serial mode is a crucial stage that must not be neglected.
The sine qua non condition for the sustainability of an SPC project is that Production, operators, adjusters and the workshop manager are responsible for the system: the SPC must be considered as a production tool and not as a constraint. Be careful to include production in the deployment project from the beginning of the project phase to facilitate the handover.
Use of an adapted, simple and fast software
By using high-performance software that is well integrated into the existing system, production work will be facilitated (automatic measurements with connected instruments, drawing of the part and dynamic guidance of the operator during the inspection run, real-time alerts in the event of a drift or alarm, etc.).
The appropriation of the software by the operators is essential to the success of the transfer.
The software will make it possible to standardise uses and representations (control charts, statistical indicators, alert rules, etc.).
The acquisition of measurements must be carried out either by connecting the checking fixtures, or automatically by file transfer, or manually by the operators.
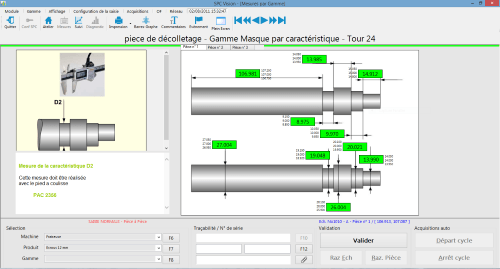
Consolidation of the fundamentals
Integrating SPC into the company’s culture means :
- training of all stakeholders in the SPC and the chosen software
- support for your employees in managing change
- explanation of the objectives of the approach
- appropriation of SPC vocabulary (Cp, Cpk, capabilities) as elements for discussion (quality meetings, etc.)
- the appropriation of the SPC approach as a brand image (internal and external)
Promotion of the work of the production teams
- Daily or weekly review of a few minutes in the workshop, motivation of the teams, emulation of the workshops, ideas for improvements, gains obtained, standardisation of the machine park following an event, etc.)
- Presentation of success stories and their actors
- Presentation of maps, histograms, evolutions, type of alarms, Pareto, indicators… (a few minutes per day allow you to be more reactive and efficient in the reporting of information!)
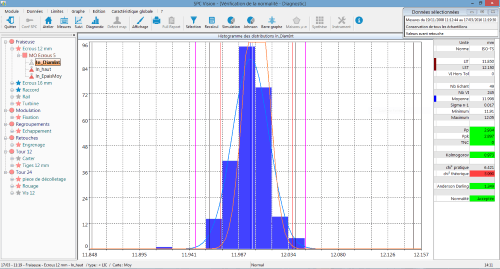
SPC as a business objective
Empowerment of each individual
Each sector is responsible for the whole chain, not just its own area…
From the design stage, integrate your machine capabilities, communicate between departments, which does not mean picking up the phone to deal with a request, but going to the workshop, talking to people, understanding their jobs, their needs, … and acting in the company’s direction.
The design office must take into account the notions of capability but must also ensure that the tolerances indicated on the drawings are indeed « realistic » in relation to the constraints of production.
Between theory and practice…it’s always the same story! We all know this only too well…
« Theory is when you know everything and nothing works. Practice is when everything works and nobody knows why. Here we have combined theory and practice: Nothing works… and nobody knows why! »
Albert Einstein
Designate a referent
Operators, adjusters and workshop managers must be responsible for it: the SPC is a production tool. Nevertheless, it is necessary to designate and appoint an SPC manager. This can be a person on the shop floor who is involved in the project and who is in a continuous improvement process, « your field leader ». He or she will be your best representative.
Communication
Invest in strong and determined communication:
- External communication towards customers, the SPC as a competitive vector
- Regular audits (internal or external) in the sense of assistance, advice
- Involvement of senior management: communication of objectives and results, integration of « SPC objectives » into objectives and individual interviews,…
Conclusion
These few elements are well known and usual, as for any classic « improvement » project in an industrial environment. Nevertheless, they must be borne in mind from the start of the project and it must be realised that the appropriation of such an approach by the production team may take time and effort, even if the resources allocated are less than during the project phase.
By defining from the beginning of the project or as soon as possible the person who will be in charge of the relay, you will perpetuate your SPC approach.
Frédéric Henrionnet
CT Infodream