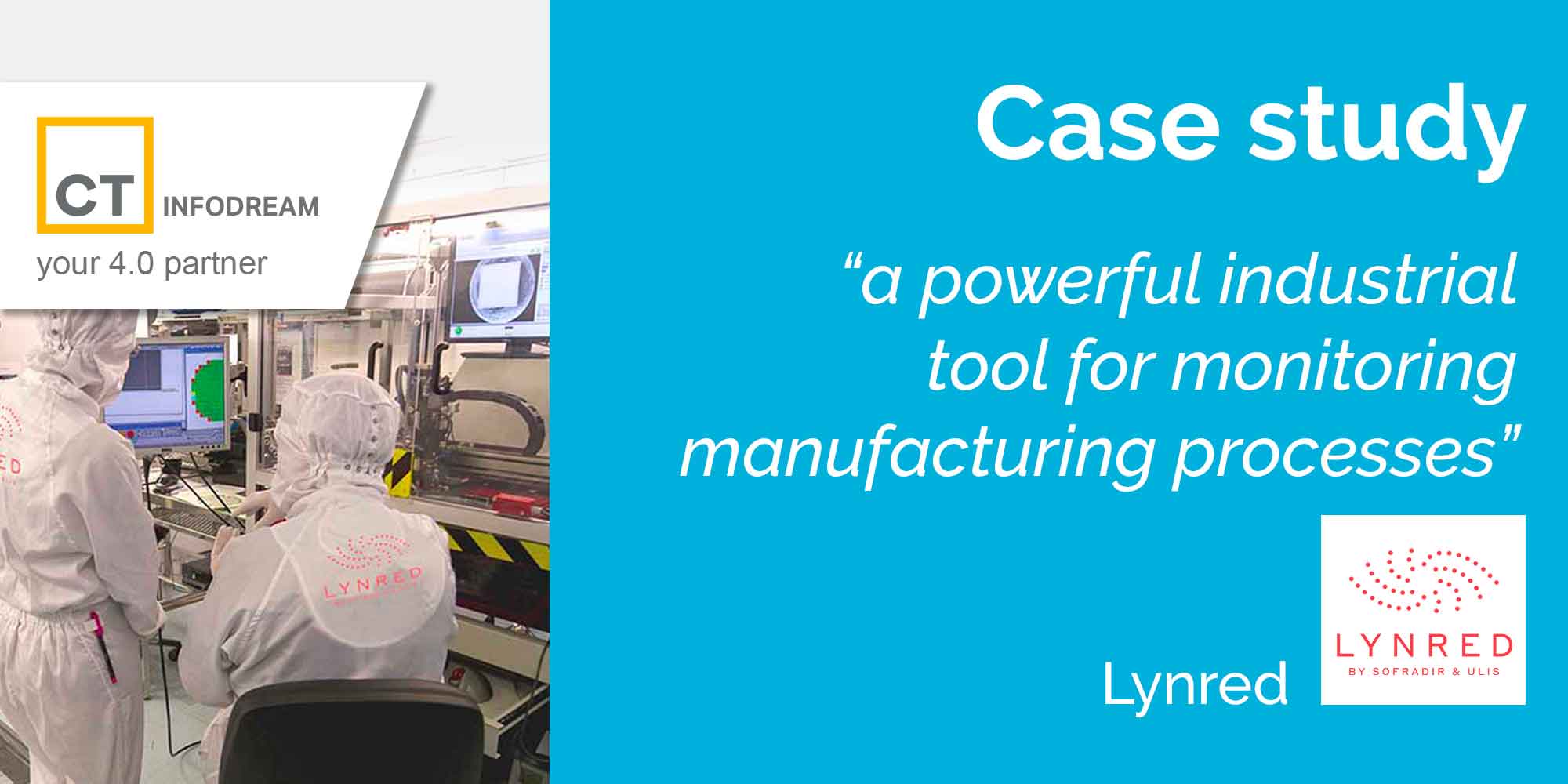
Lynred case study
For LYNRED, continuous improvement is a never-ending road…
Vincent De Schuyteneer, data expert engineer at LYNRED, explains how his company is constantly improving its manufacturing processes with the Qualaxy SPC software.
Who’s LYNRED?
LYNRED and its American subsidiary LYNRED USA are world leaders in the development and production of high quality infrared technologies for the aerospace, military, industrial and consumer markets. Their vast catalogue of infrared detectors covers the entire electromagnetic spectrum from near to far infrared. Their products are at the heart of many military programs and applications. These IR detectors are key components of major commercial brands of thermal imaging equipment sold in Europe, Asia and North America. The company is the European leader in IR detectors deployed in space..
Why choose CT INFODREAM’s solution?
In order to guarantee our customers state-of-the-art products, it was essential to implement a powerful industrial tool for monitoring manufacturing processes.
« This is why LYNRED (born from the merger between its two historical entities ULIS and Sofradir) chose to deploy the SPC methodology with the Qualaxy SPC tool. We chose this tool for 3 main reasons:
-
- its flexibility of use,
- the trust established with CT INFODREAM,
- the geographical proximity between our two companies.
When the project started on the Sofradir side, the members of the project team made the choice of full integration within the information system, based on the experience gained by ULIS. This integration allowed the automatic transfer of data from the data generation systems (process equipment, measuring equipment or MES) to Qualaxy SPC, and vice versa the transfer of alerts to the MES (in case of out-of-control or drift), thus making it possible to block the incriminated process equipment, thus applying the Jidoka principle of Lean Manufacturing, i.e. shutting down as soon as a malfunction occurred.
In addition, Qualaxy SPC also allows us to monitor our production and metrology equipment through regular monitoring on standardised specimens adapted to our needs. This monitoring also guarantees our customers a production according to pre-established and rationalized quality rules. »
A solution that was quickly adopted by the various trades.
The operators very quickly adopted this new tool, which enabled them to see the evolution of production in real time and to immediately escalate problems to the support/engineering department.
Vincent De Schuyteneer,
Data Expert Engineer at LYNRED
www.lynred.com