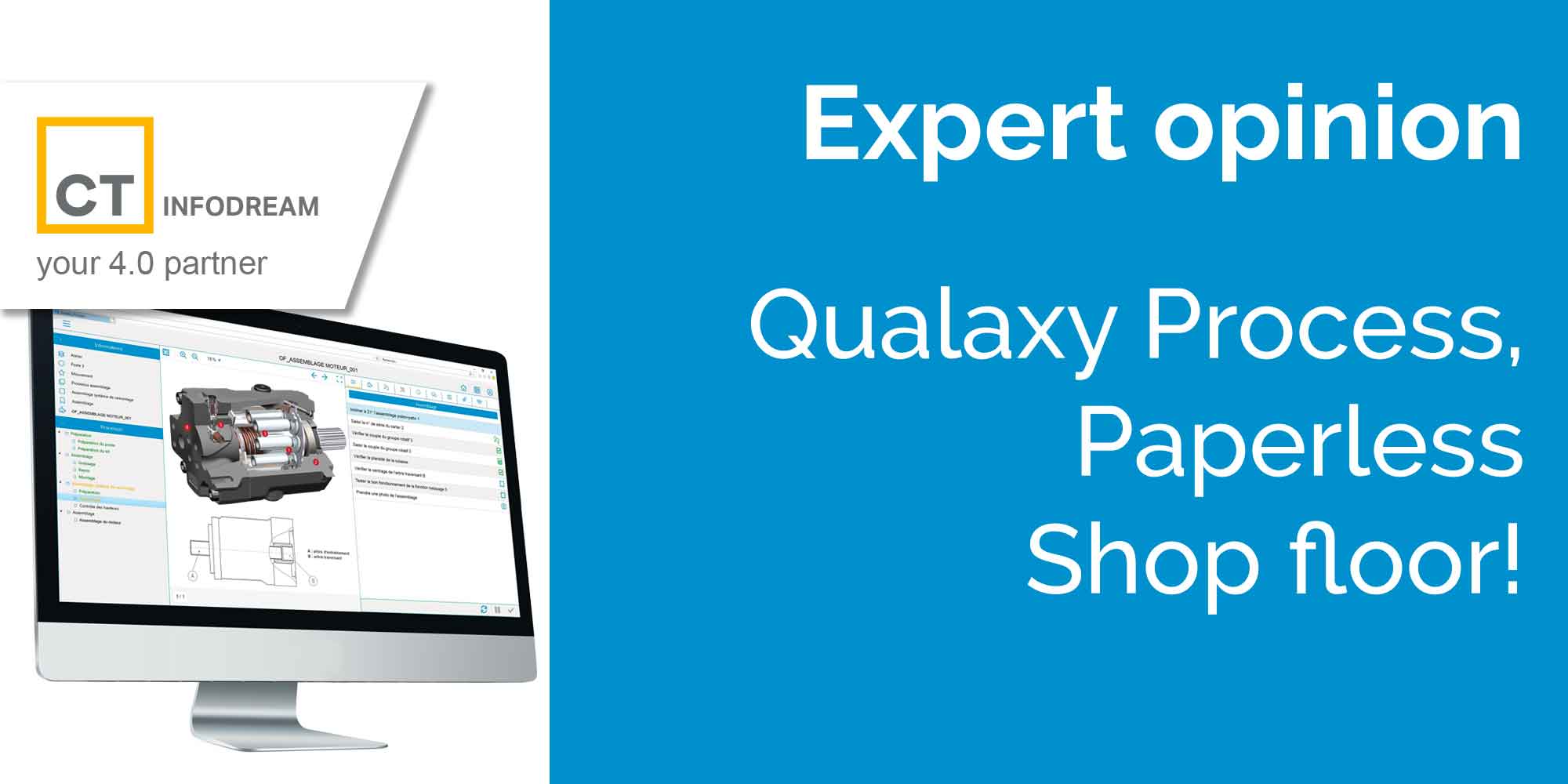
Qualaxy Process, Paperless Workshop!
The Paperless workshop! The ultimate goal (or dream) for any production manager!
But, is it possible or even desirable? If so, how – and at what cost?
Why the paper?
This is the first question to ask. What is the purpose of paper, and what do I do with it?
Firstly: Operator work instructions
These are explanatory documents on how to set up the process, what tools to use, what checks to make, safety precautions etc..
To be useful, these instructions must be at the workstation where the task is being done. They are physical documents so need to be printed but also stored using cupboards, filing cabinets etc.
With any paperwork, the availability of the document is highly questionable and assuming it is available, Is it up to date? Is it the correct version which matches the product on which it is being used?
Secondly: Inspection Checksheets – documents for recording data
In manufacturing, automated or manual, many items need to be recorded, everything has to be noted, commented, registered in order to demonstrate that the product and manufacturing process conforms to the specification and the process fully traceable. This information must be safely stored and easily retrievable!
Due to regulatory standards, some industries are culturally more advanced than others in this respect (aerospace, medical, …) but today, there is no workshop free from this requirement.
It is very common to need to record things such as:
- Process data (Machine id, settings, parameters, tool id etc)
- Product measurements (at many stages of manufacturing)
- Raw material (batch numbers, supplier, storage environment, etc)
- Operator id
The first findings are obvious:
- All in all, this adds up to a very large amount of paperwork on the shop floor. For some complex products, there is a sizeable folder full of instructions, check-sheets, drawings and other documents for every single unit!
- Historically, what could be easier than using paper and pencil to track parts! But these days, only having a paper copy is too limited since we want to analyze and report the data (customer reports, SPC, ERP link etc …). Therefore, the data is re-entered manually into a computer!
The second question to ask is “how to become a paperless workshop?”

We can decide to have documents in digital format using PCs or tablets in the workshop.
For work instructions, the solution is easy: a computer station, a catalogue of procedures and instructions and minimal training for the operator.
However, we can make two observations:
- you can never be certain that the operator opens, reads and follows the correct document
- installing a computer station (or tablet PC, wired or wireless) has a cost (so you want it to be more than an expensive reading light!)
If you simply change the paper document or check sheet into an electronic document which is completed on the shop floor, then the question of re-entering data is answered. However, this does not add value to the operator: he simply will write or check using a computer instead of using a paper and pencil.
The right attitude: how to intelligently automate the workshop?
A new approach is needed which fulfils all of the above tasks and requirements but also addresses the many problems associated with the paper system. Above all, this new type of system should add value and help in the pursuit of increased quality and reduced manufacturing costs!
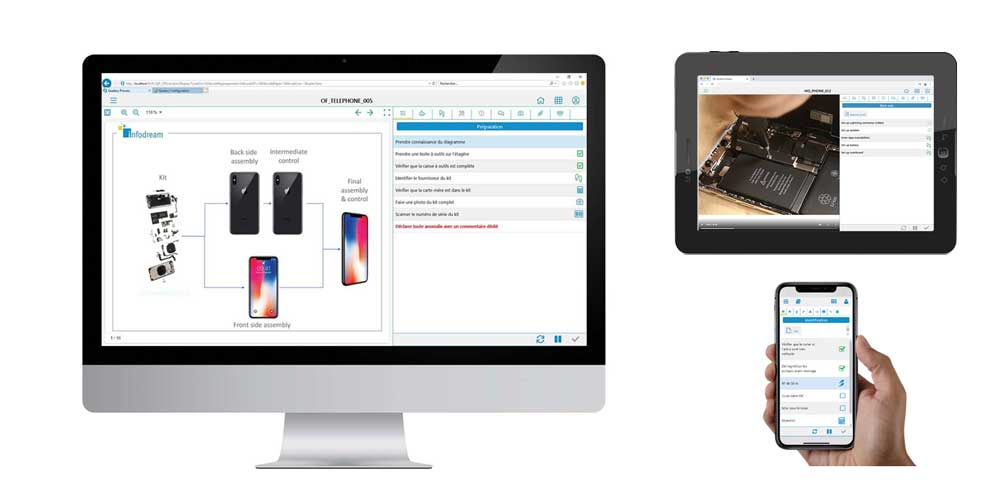
Paperless Workshop: our Solution
Without going into too many details, our Qualaxy Process software meets these needs.
The system is designed around the process and how the operator will work through it.
The operator screen is divided into 3 zones:
- The process plan – operations and steps
- Explanatory instructions
- Execution and data recording (checks, measurements, traceability)
The key point is that for each operation, the operator is only presented with the specific information for the step in which they are working on. This drastically simplifies things from the operators point – it is very clear what they need to do, exactly how to do it and what must be recorded. Operator error is drastically reduced and compliance to the defined process is achieved.
The operator has real time feedback: he can be asked to enter certain measurement values (conforming / non-conforming return), certain traceability fields (raw material batch number, equipment number: return validity or expiry). The software will also help with times: process, operating and rest times, etc.
Provision of Work Instructions for operators (via Qualaxy Process) requires a change in attitude:
They should not be generic or rough guidance (informal)
- Clarification of the process
- Explicit description of each process action
- Standardisation of processes
They promote confidence
- All process actions are fully traceable – who, what, when
- Process times and breakdown are recorded and analysed
They are interactive
- The documentation is progressing with the operator workflow
- The system ensures data collection (checks, measurements, traceability)
They are part of a ‘global’ shop floor information system
- Process conformance
- Process control
- Shop floor production management – tracking work orders etc.
With the paperless workshop, traceability becomes native and intrinsic: we know who checked what and when!
Frédéric Henrionnet
CT Infodream
Learn more about Qual@xy Process