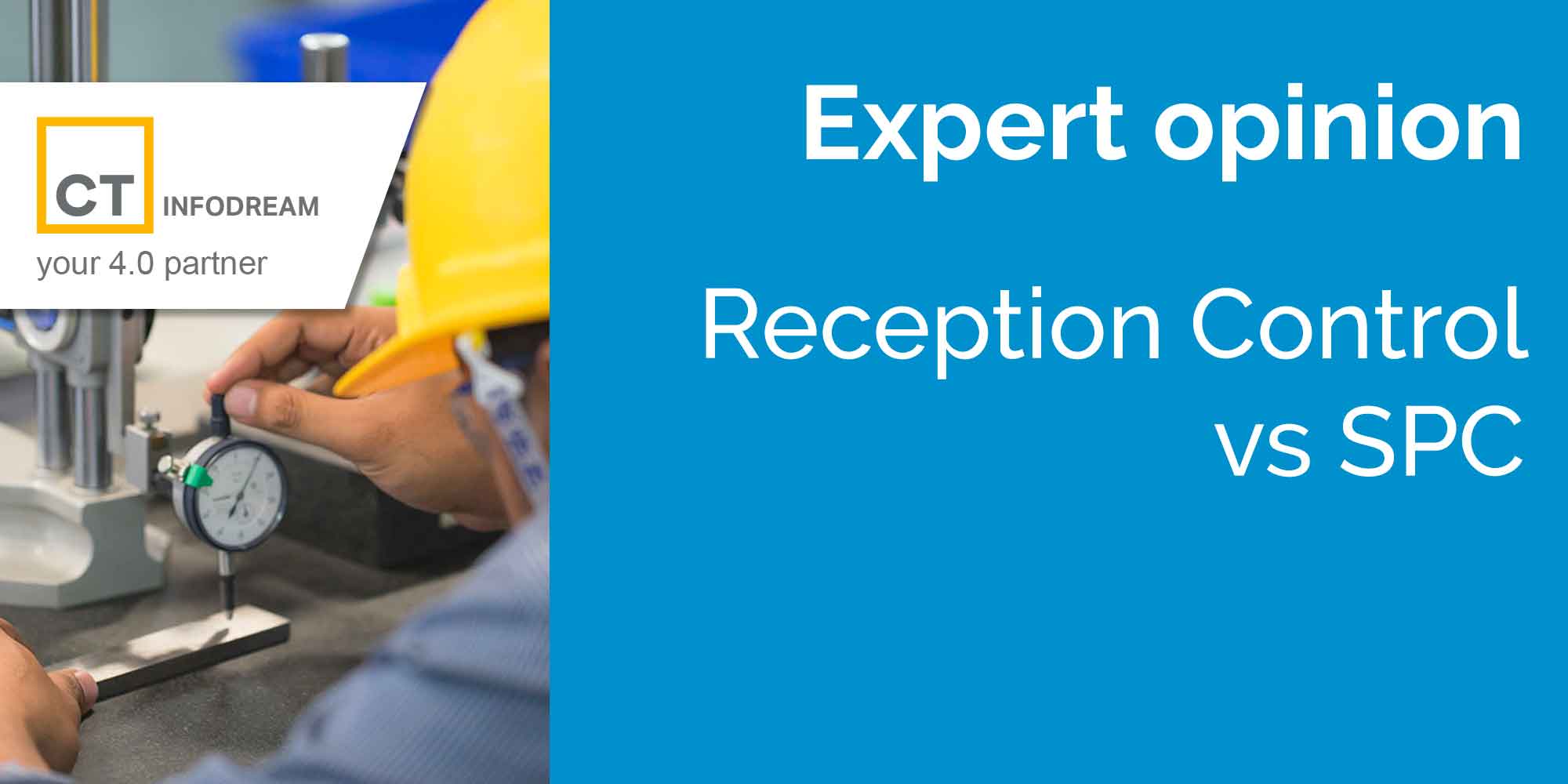
Reception Control vs SPC?
In this article, we will discuss two concepts in the field of Quality: incoming inspection and SPC. What links exist between the two? What are the common functions? Reception control vs SPC, let’s go!
Reception control and SPC functions
We often separate incoming inspection (incoming inspection of purchased parts and components) and SPC inspection (in-process inspection of manufactured parts). These are not the same references, nor the same people (inspectors in the first case, operators in the second), nor often the same inspection locations (laboratory or workshop). But the finished product manufactured and assembled by the company does include these two types of parts. Should we therefore continue to oppose these two functions, and above all continue to dissociate these two types of measurement data?
What is the reception control?
The incoming inspection (or incoming inspection, incoming inspection) makes it possible to accept or reject a batch of parts from a supplier (usually external, but also internal). This stage is very important. Indeed, refusing a batch can lead to a shortage of material in the workshop (especially if you are on a just-in-time basis). Accepting a batch containing potentially non-compliant components can also cause a quality crisis in the rest of the process.
Read also What is the reception control?
Incoming inspection: supplier monitoring and reporting
The basic unit of incoming inspection is the batch of parts.
But just as the objective of the SPC is to move from a « part conformity » vision to a « statistical evolution » vision, a Reception Control software must manage the evolution over time of the different acceptances, of the different suppliers, etc. It must therefore propose a complete reporting: summary table of batches, suppliers, evolution of the percentages of refusals per period of time, etc. It must therefore offer complete reporting: summary table of batches, suppliers, evolution of refusal percentages per period of time, etc.
Documentary editing is therefore important. Depending on a batch refusal report, a supplier may have to start quality actions or even be downgraded.
Interest of a common SPC and Control database
There are therefore many functions and concepts that are common to both the reception control and the SPC :
- Moving from a conformity vision (batch/piece) to a statistical vision (evolution over time)
- Notions of centring and dispersion (my batch is accepted, of course, but is it well centred? Grouped together? Dispersed? What will be the impact on the final assembly?)
- Punctual reporting (PV on a batch/PV on a part) in parallel with temporal reporting (by time period)
- Definition of inspection plans, incoming inspection and/or SPC
- Notion of SPC or ISO alarms (refusal of a batch)
- Enabling/submission ranges to be compared with green light/production ranges, etc.
- Process and measurement means, repeatability, reproducibility, etc.
But the most important thing is that these purchased components will be used to manufacture or assemble a part or sub-assembly, the final characteristics of which will depend on both the « supplied » and « manufactured » parts. In incoming inspection, there is no notion of real time reaction, to go and adjust the process as soon as possible. But once the measurements have been taken, why not use them to adjust the assembly processes? To shift manufacturing IT when possible? To carry out pairing not by part, but by batch? To detect long-term drifts that are independent of the production itself?
Having a single database means that product references can be defined only once, even if they may have « manufactured » dimensions (and monitored in SPC), and others « purchased » (and monitored in incoming inspection). It will be possible to pool results, changes, make correlations, etc..
In a word, we will be able to better control our process…
Frédéric Henrionnet
Quality Assurance Manager at Infodream
Learn more about Qualaxy Control Software
See the advanced functions of Qualaxy Control software
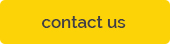