![Starting A SPC Project [3/4]](https://infodreamgroup.com/wp-content/uploads/2018/02/starting-spc-project-3-ct-infodream-mes-spc-msp-2000x1000-1.jpg)
Starting a SPC Project [3/4]
During part 2 of this short series I highlighted the importance of having a structured process to ensure the success of the SPC project. During this final part, I’ll outline some of the key components and consideration for each step.
1. Business Case
SPC is one of those topics where almost everyone will agree that it is a good thing and know the general benefits such as improved process control, reduced waste, empowering operators etc. However, any project will have an associated cost and these qualitative statements don’t cut it with the financial guy’s when you need a budget for the project!
A poor business case is the reason why many projects fail to even get off the ground. However, there are many benefits which can be quantified and the return on investment of a SPC project is normally relatively fast.
The benefits should be considered using a fishbone type approach and broken down into categories such as:
- Quality / Waste Improvement – Scrap, rework, concession etc.
- Production Easement – lighten inspection frequency, optimise maintenance etc.
- Organisation – Real time analyse reduces engineer analysis time etc.
- QMS – If SPC software is used there are many additional QMS benefits including reduced audit time, tighter control of documentation, reduced human error etc.
The critical point in the business case is not only having a good ROI but ensuring that the benefits are linked directly to the overall business objectives. Otherwise you will not receive the support needed. I have a more detailed document which we use to calculate SPC benefits. Please email me if you would like to receive a copy.
2. Senior champion
Finding a senior champion could be the first step of the project but already having a business case can’t hurt. A good focused project champion is the single most important element in determining the success of the project. There are many famous ‘top level’ champions such as GE’s Jack Welch but unless you are deploying a company wide initiative you need someone a little lower down the food chain!
Basically you need someone who has some cross functional responsibility. Generally this could be the plant manager or maybe the business unit manager. The champion will ensure all of the various stakeholders are fully engaged, attend high level project reviews, remove obstacles and generally ensure the project stays on track and delivers the benefits.
3. Strategy including KPI’s (Key Performance Indicators)
We touched on this topic during part 2 and there are various ways in which SPC can be deployed ranging from small pilot project to full company-wide roll-outs. Either way, it is important that there is a both a clear strategic and deployment plan. The plan will form the backbone for driving and monitoring the project. This should document the overall business benefits defined in the business case, how these flow down into specific key performance indicators (KPI’s). It should also specific the various stakeholders and their roles and responsibilities. The deployment plan should include the time frame for each of the project elements.
A key part of the strategy is to ‘sell’ the project to all the stakeholders. Although the project may eventually be forced onto them by the champion it is far better for the project to be ‘pulled’ rather than ‘pushed’. This can be achieved by running some basic manager training workshops and by ensuring the KPI’s have clear benefit for each stakeholder.
4. Cross Function Business Process
This is again a key point and an area where I have seen many projects fall down. As with all other processes in your business there are many different people involved, with different roles and responsibilities. For a SPC project we are generally talking about Operations, Engineering, Quality, Design and IT – if SPC software is being used. IT is becoming an increasingly important stakeholder and this point will be covered in a separate blog post.
It is important that each of the people involved know what is expected of them and when action is needed. For example – a shop floor operator will probably be collecting some sort of measurement data which will be plotted onto a control chart either manually or automatically. The next question is whether the operator is responsible for analysing the charts for special causes? If so, what should they do when they detect one – stop the process, call engineer/supervisor or do nothing? It is important to document these processes and ensure everyone understand them. The SPC process and related procedures should form part of your quality management system (QMS). Please contact me if you would like to see some examples of these documents.
We are starting to see that setting up a successful SPC project is not as straight forward as simply putting a control char tout on the shop floor. However, it needn’t and shouldn’t be too complicated either. Next time I’ll cover the final 3 points in this series.
Ben Allister
Director Infodream UK
Read the previous article: Starting a SPC Project [2/4]
Read the next and last article: Starting a SPC Project [4/4]
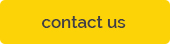