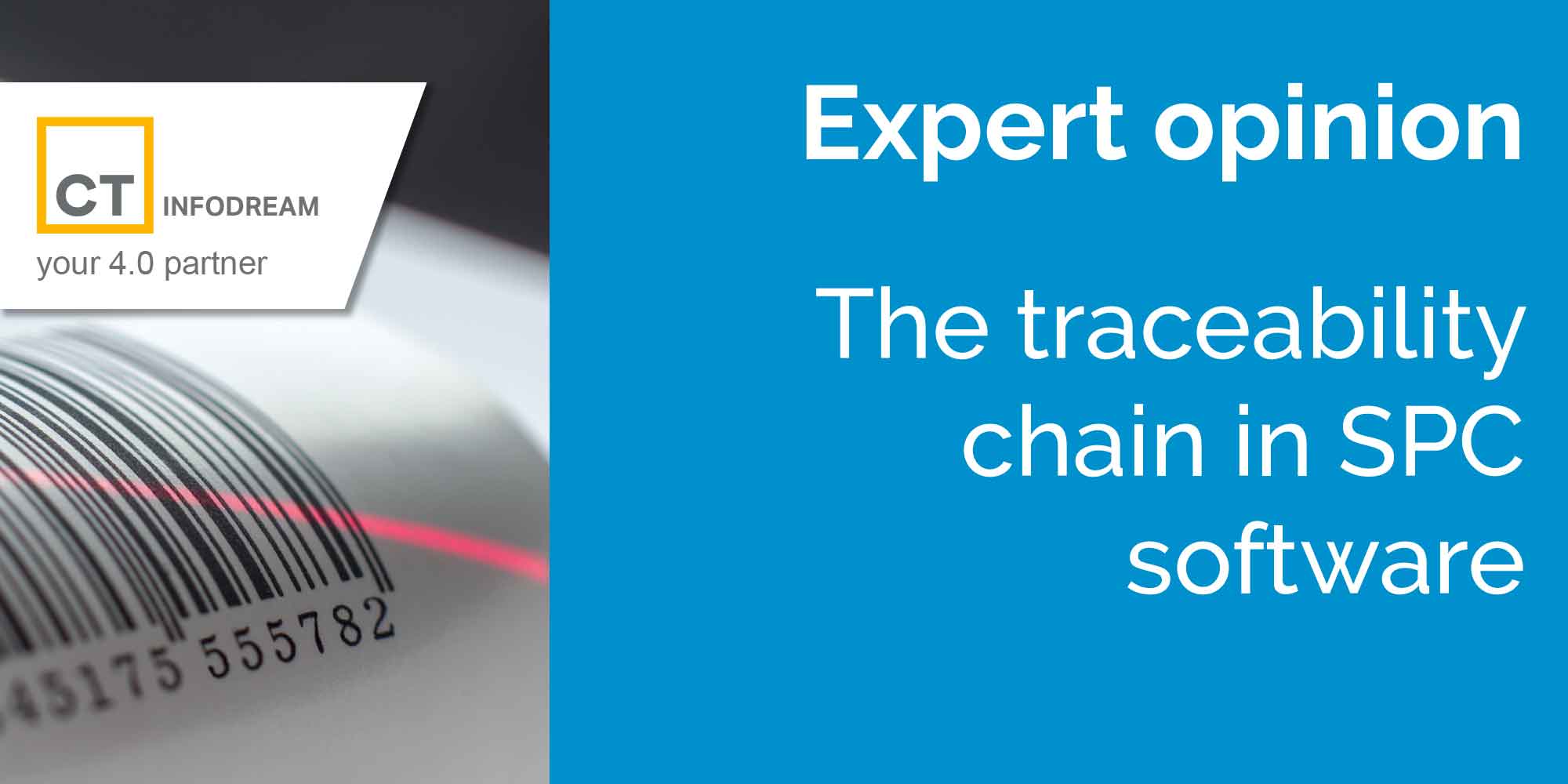
The traceability chain in SPC software
In this article, we define the concept of traceability. Then we explain with examples the different types of traceability to be identified during long and complex manufacturing processes.
What is traceability?
Traceability is an important concept, even critical in certain processes. For the food and pharmaceutical industries, of course, but also for the aeronautical industry and more generally for all industrial production.
Definition of traceability
« Traceability refers to the situation where the necessary and sufficient information is available to know the composition of a material or product throughout its production and distribution chain » (Wikipedia).
In other words, « from the cradle to the grave », or « from the fork to the spoon »..
Chain of Custody
The traceability chain is important in SPC modelling. It allows the comparison (or correlation) of monitored characteristics of a part or sub-assembly at different stages of the manufacturing process. For example, very early in the process, then later in the final inspection.
The serial number (SN): the simplest traceability
The simplest and most immediate traceability is of course the identification of the part. This is the serial number (or rank number, MSN). All the measured characteristics are linked to a single identifier, and there is no risk of error.
This identification by SN (Serial Number) is used in processes with high added value. For example in aeronautics, precision machining, watchmaking, etc.
In mass production, we tend to talk about batch numbers or OF numbers for a series of parts. Several tens, hundreds or thousands of parts, for example, for baskets of bar turning parts.
If the traceability follows the manufacturing process and we know that an identified batch has passed through the OP10 and then the OP20, we will be able to correlate the X dimension of the OP10 with the Y dimension of the OP20. But we will be comparing distributions and statistical values instead of comparing individual measurement values.
If I measure the same characteristic at 2 stages of my process, how can I identify it?
The answer is very simple: it is not the same feature!
Example 1: I have a roughing operation where I measure a dimension, and I measure the same dimension two operations later, in finishing.
Example 2 : I measure a dimension before and after a heat treatment.
It cannot be the same dimension as there may be different targets or tolerances. For example, a machining allowance is left at the roughing OP.
In this case, it is very important that the Methods department provides Production with a manufacturing plan by phase, with the target dimensions for the current OP.
If a « finished dimensions » plan is provided to production, the operator must add an oversize on his own. Or position himself on the strong side of the dimension to be sure to respect the final tolerances. In this case, no statistical monitoring will be possible.
Remark: we will take the opportunity here to ask for manufacturing drawings with centred targets. Indeed, a 12.00 +0.05 +0.01 dimension is of no interest to a setter.
How to correlate characteristics measured independently on a sub-assembly with characteristics measured on a final assembly?
The answer is also very simple: use assembly traceability.
- We measure the score X on the subset of SN n°12.
- Then the Y dimension is measured on the final assembly of SN n°23-B.
- It should then be drawn that the final part n°23-B is assembled with the sub-assembly n°12.
- So we can correlate the X dimension and the Y dimension on the final assembly !
This requires the use of software that allows comparison using this assembly traceability.
Note: this also requires the operator to enter the SNs of the components during assembly.
When using elementary components, these are often not identified individually but only by batch.
It is important to trace this batch number and to be able to use the reverse traceability function. This means that it is possible to identify the final assemblies assembled with a particular component.
For example, during a control operation (during the process or for a customer return), it is discovered that an elementary component is defective. From the serial number of the finished part, we can identify the batch number of this defective component.
And thanks to reverse traceability, we will be able to find all the parts that have been assembled with a component from this batch.
But how do you attach measurements to a room that does not yet exist?
This question may arise when the Serial Number is created very late in the process.
The answer is more delicate because we will have to « create » a chain of traceability. This involves decisions at the organisational, methodological and logistical levels…
Example :
In foundry: the part exists and is identified when it is cast. The entire upstream process (moulding – core making – remoulding) cannot be attached to a part that does not exist.
The solution in this case is to create an « arbitrary » traceability (or to use an OF number, a logistics number or an order number) and to attach all the « upstream » measures to it.
This arbitrary traceability must then be linked to the identification of the part via the assembly traceability function.
This idea works very well, even for measurements that are relatively disconnected from the part manufacturing process. One can very well attach measurements to an identifier manufactured with the day of the month for example, and attach this identifier with the assembly traceability.
Example :
In plastic injection moulding on large serialised parts, daily checks are carried out on the material to be injected (particle size, temperature, composition, etc.). These checks are attached to a unique day identifier (2020-124, 2020-125, etc.) and this number is itself attached to the injection identifier. We could go back to the material quality for an aspect defect identified on a part by passing through the deadline number.
In conclusion
The chain of custody is a critical notion for any SPC system that has to follow a somewhat long and complex manufacturing process.
This reinforces the idea that an SPC project is a structuring project. It requires the involvement of everyone, from the operator and the controller to management and logistics.
For its success, an SPC project must be considered as a company project. It must have a sponsor from General Management and of course a recognised « business driver » in Methods or Quality.
Frédéric Henrionnet
Quality Assurance Manager at Infodream
Screenshots from Qual@xy SPC software
