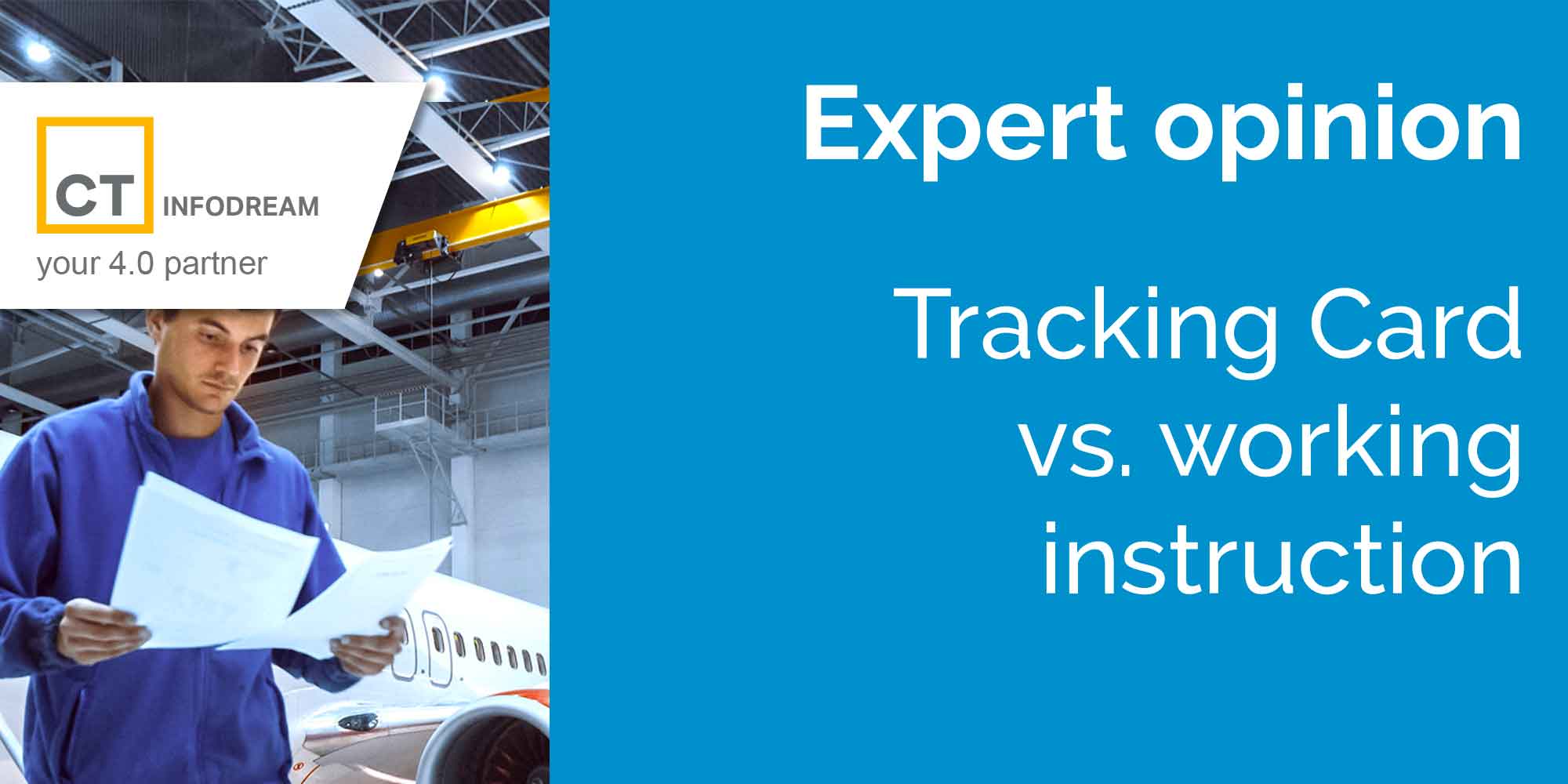
Tracking Card vs. working instruction
The documents present in the production workshops
Various types of documents are present on the production floor.
These are:
regulatory documents:
- safety instructions,
- instructions for use…
technical documents
- manufacturing ranges, setting ranges
- dimensioned drawings
- work instruction (WI); it describes what to do and how to do it
traceability documents
- Tracking sheet (TS); it guarantees the traceability of the part or the Work Order (WO)
Traceability documents
The work instruction is a descriptive document only.
It describes the operating process as precisely as possible. It contains diagrams, photos, videos, diagrams, steps, instructions, lists tools, equipment, PPE, components, etc. Although it is present throughout the operation, it is not intended to capitalise on information but remains the guarantor of factory « know-how ».
The tracking sheet is a capitalization document.
The follow-up sheet lists the points to be checked and is used to trace information relating to the OF (identification of components, equipment, tools, PM, etc.).
Present throughout the operation, it must be archived at the end of the OF as it guarantees that the correct verification of critical data has been carried out.
A computerised tracking sheet becomes part of the company’s MES or ERP software.
The links between the work instruction and the follow-up sheet
Example 1
- Work instructions: glue A to part B. Check that the gap between A and B is > 5mm.
- Tracking sheet: batch number of glue used + expiry date. Measurement of the gap between A and B.
Example 2
- working instructions: tighten screw no. 8 with a torque wrench of 8 Nm
- Tracking sheet: identification number of the screwdriver used + date of last calibration.
Here we mix description (what needs to be done) and traceability (what needs to be controlled). The work operation then becomes an imposing paper file with a large number of pages.
The mixing of process description and control can also be questionable. A work instruction and a follow-up sheet can be either:
- independent: we want to check the gap between A and B. The measurement is then independent of the means of assembly (glued or screwed)
- strongly linked: A and B are glued. In this case it is important to keep track of the expiry date of the glue pot. This makes no sense if instead of gluing, you screw A and B together.
Work instructions and tracking sheets must therefore always be created and modified « in parallel ». However, these 2 documents are of a different nature and, even worse, are often written by 2 different teams:
- The work instruction is written by the preparation team = « What to do »
- The follow-up sheet is drawn up by the quality team = « What to check »
Moreover, there is no quantitative relationship between the two:
- a complex operation may require 5 pages of description but no traceability
- a simple operation may require numerous entries tracing aspect quality and dimensional tracking
The solution that we, Infodream, recommend
Rather than having a long and cumbersome document mixing both know-how and traceability, we recommend dissociating these two notions:
- a description of the process, which will explain, describe and show what needs to be done and how it should be done, including video explanations if necessary
- a traceability input part, which will capitalise everything that needs to be checked and validated for each operation or each production phase (simple validations, traceability, component identification, parameter input, etc.)
These two « parts » must therefore be synchronised and move forward in parallel: therein lies the secret!
The operator no longer needs to leaf through his work document as he is provided with the right information at the right time. The operator is guided in the sequence of his actions, minimising the risk of « switching » errors or omissions and allowing him to focus on the quality of his operation, which is where all his added value lies.
The integration in the MES software is obvious: we add a page allowing to visualize the state of progress of the OFs, of the parts, to type the causes of interruptions (global vision of the state of the workshop…) and we obtain a solution which allows to advance towards the 0 paper in the workshop.
Frédéric Henrionnet
CT Infodream
Learn more about: Qual@xy Process, to digitise your processes